Method for manufacturing composite Raman-enhanced substrate
A substrate and solution technology, which is applied in the field of preparation of composite Raman-enhanced substrates, can solve problems such as poor repeatability and stability, easy vulcanization and oxidation, and unstable chemical properties, and achieve excellent performance, enhanced stability, and enhanced Raman enhancement. performance effect
- Summary
- Abstract
- Description
- Claims
- Application Information
AI Technical Summary
Problems solved by technology
Method used
Image
Examples
Embodiment 1
[0020] 1. A 30nm thick Ag discontinuous nano-film was prepared on a smooth substrate by magnetron sputtering;
[0021] 2. Prepare 20ml of K2PtCl4 solution with a concentration of 0.1mM and 20ml of C6H5Na3O7 solution with a concentration of 0.15mM, and stir thoroughly;
[0022] 3. Put the nano-Ag film substrate prepared in step 1 into the solution prepared in step 2, react at 90°C for 25 minutes, take out the substrate and wash it;
[0023] 4. Prepare 20ml of 10wt% hydrogen peroxide, put the substrate into it, stir and react for 8 minutes, take it out and wash it;
[0024] 5. Prepare 20ml of 0.2mM NaBH4 solution, put the substrate into it, stir and react for 6min, take it out and wash it.
[0025] The SEM image of the prepared composite Raman-enhanced substrate is shown in figure 1 , the substrate is used for 0.001mM rhodamine test, the performance diagram is as follows figure 2 shown.
Embodiment 2
[0027] 1. Prepare a 20 thick Ag discontinuous nano-film on a smooth substrate by magnetron sputtering;
[0028] 2. Prepare 20ml of K2PtCl4 solution with a concentration of 0.05mM and 20ml of C6H5Na3O7 solution with a concentration of 0.05mM, and stir thoroughly;
[0029] 3. Put the nano-Ag thin film substrate prepared in step 1 into the solution prepared in step 2, react at 90°C for 10 minutes, take out the substrate and wash it;
[0030] 4. Prepare 20ml of 10wt% hydrogen peroxide, put the substrate into it, stir for 5 minutes, take it out and wash it;
[0031] 5. Prepare 20ml of 0.2mM NaBH4 solution, put the substrate into it, stir and react for 5min, take it out and wash it.
Embodiment 3
[0033] 1. Prepare a 50nm thick Ag discontinuous nano-film on a smooth substrate by magnetron sputtering;
[0034] 2. Prepare 20ml of 0.5mM K2PtCl4 solution and 20ml of 1mM C6H5Na3O7 solution, and stir thoroughly;
[0035] 3. Put the nano-Ag film substrate prepared in step 1 into the solution prepared in step 2, react at 90°C for 30 minutes, take out the substrate and wash it;
[0036] 4. Prepare 20ml of 10wt% hydrogen peroxide, put the substrate into it, stir and react for 10min, take it out and wash it;
[0037] 5. Prepare 20ml of 0.2mM NaBH4 solution, put the substrate into it, stir and react for 10min, take it out and wash it.
[0038] The composite Raman-enhanced film substrate prepared in the above examples has a simple preparation process, excellent performance, good stability, and good practicability.
PUM
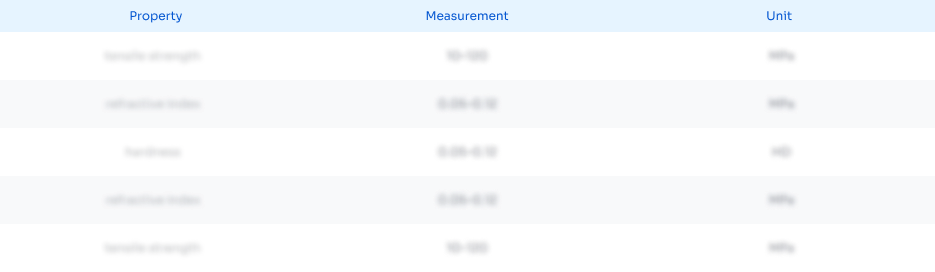
Abstract
Description
Claims
Application Information

- R&D
- Intellectual Property
- Life Sciences
- Materials
- Tech Scout
- Unparalleled Data Quality
- Higher Quality Content
- 60% Fewer Hallucinations
Browse by: Latest US Patents, China's latest patents, Technical Efficacy Thesaurus, Application Domain, Technology Topic, Popular Technical Reports.
© 2025 PatSnap. All rights reserved.Legal|Privacy policy|Modern Slavery Act Transparency Statement|Sitemap|About US| Contact US: help@patsnap.com