Forced cooling of chassis and method thereof
A technology of forced cooling and chassis, applied in the field of forced cooling chassis and forced cooling, can solve the problems of easy burning and deformation, easy burning, shortening the service life of steel ingot chassis, etc., and achieve the effect of reducing cost and simple process
- Summary
- Abstract
- Description
- Claims
- Application Information
AI Technical Summary
Problems solved by technology
Method used
Image
Examples
Embodiment Construction
[0058] The above and other technical features and advantages of the present invention will be clearly and completely described below in conjunction with the accompanying drawings. Apparently, the described embodiments are only some of the embodiments of the present invention, not all of them.
[0059] see Figure 1 to Figure 3 As shown, a forced cooling chassis of the present invention includes a bottom plate 10 and a composite plate 20 stacked on the upper surface of the bottom plate 10 . A pouring hole 22 and at least two drain holes 24 arranged around the pouring hole 22 are provided on the composite plate 20, the pouring hole 22 and the drain hole 24 are separately arranged, and the pouring hole 22 and the drain hole 24 all pass through the composite plate vertically 20. At least two molten steel grooves 12 extending from the pouring holes 22 to the drainage holes 24 are provided on the upper surface of the bottom plate 10, and the pouring holes 22 and the drainage holes ...
PUM
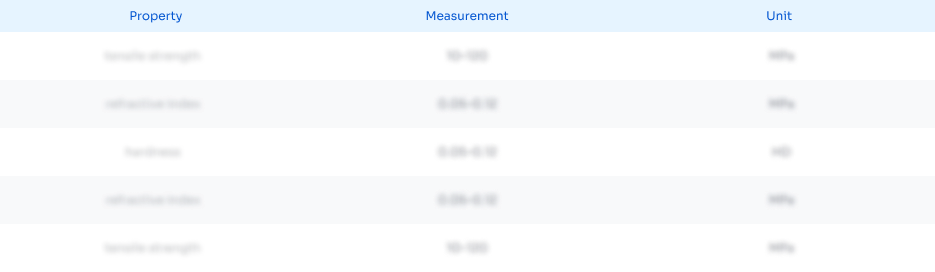
Abstract
Description
Claims
Application Information

- R&D
- Intellectual Property
- Life Sciences
- Materials
- Tech Scout
- Unparalleled Data Quality
- Higher Quality Content
- 60% Fewer Hallucinations
Browse by: Latest US Patents, China's latest patents, Technical Efficacy Thesaurus, Application Domain, Technology Topic, Popular Technical Reports.
© 2025 PatSnap. All rights reserved.Legal|Privacy policy|Modern Slavery Act Transparency Statement|Sitemap|About US| Contact US: help@patsnap.com