Preparation method for vanadium phosphorus oxide catalyst used in selective oxidation of hydrocarbon
A technology of vanadium phosphorus oxide and catalyst, applied in physical/chemical process catalysts, chemical instruments and methods, organic chemistry, etc., can solve the problems of poor strength and poor heat dissipation of VPO catalysts
- Summary
- Abstract
- Description
- Claims
- Application Information
AI Technical Summary
Problems solved by technology
Method used
Examples
Embodiment 1
[0030] Add 5g of tungsten carbide fine powder into 50ml of 2M phosphoric acid solution, stir and heat to 80°C and maintain for 3h. The resulting precipitate was filtered and washed with water, and then dried at 120° C. for 10 h to obtain phosphoric acid-treated tungsten carbide. Add 25g of vanadium pentoxide and phosphoric acid-treated tungsten carbide powder into a mixed solution of 250ml of isobutanol and 100ml of benzyl alcohol, start stirring and slowly add about 30.8g of 105wt.% phosphoric acid, heat the mixed solution to reflux and then reflux for 16h, stop After heating, the mixed solution was filtered and washed with isobutanol, and the resulting filter cake was dried at 120° C. for 20 h to obtain a precursor. The precursor was calcined at 250°C for 3 hours in an air atmosphere, then heated to 425°C for 3 hours in an atmosphere with a volume ratio of 20% air / 20% nitrogen / 10% carbon dioxide / 50% water vapor, and finally baked at 40% nitrogen / 10% The active catalyst was ...
Embodiment 2
[0036] Add 5g of tungsten carbide fine powder into 50ml of 2M phosphoric acid solution, stir and heat to 80°C and maintain for 3h. The resulting precipitate was filtered and washed with water, and then dried at 120° C. for 10 h to obtain phosphoric acid-treated tungsten carbide. Add 25g of vanadium pentoxide and phosphoric acid-treated tungsten carbide powder into a mixed solution of 300ml of isobutanol and 60ml of benzyl alcohol, start stirring and slowly add about 30.8g of 105wt.% phosphoric acid, heat the mixed solution to reflux and then reflux for 16h, stop After heating, the mixed solution was filtered and washed with isobutanol, and the resulting filter cake was dried at 120° C. for 20 h to obtain a precursor. The precursor was calcined at 250°C for 3 hours in an air atmosphere, then heated to 425°C for 3 hours in an atmosphere with a volume ratio of 20% air / 20% nitrogen / 10% carbon dioxide / 50% water vapor, and finally baked at 40% nitrogen / 10% The active catalyst was obt...
Embodiment 3
[0038] Add 3g of tungsten carbide fine powder into 50ml of 2M phosphoric acid solution, stir and heat to 80°C and maintain for 3h. The resulting precipitate was filtered and washed with water, and then dried at 120° C. for 10 h to obtain phosphoric acid-treated tungsten carbide. Add 25g of vanadium pentoxide and phosphoric acid-treated tungsten carbide powder into a mixed solution of 300ml of isobutanol and 60ml of benzyl alcohol, start stirring and slowly add about 30.8g of 105wt.% phosphoric acid, heat the mixed solution to reflux and then reflux for 16h, stop After heating, the mixed solution was filtered and washed with isobutanol, and the resulting filter cake was dried at 120° C. for 20 h to obtain a precursor. The precursor was calcined at 250°C for 3 hours in an air atmosphere, then heated to 425°C for 3 hours in an atmosphere with a volume ratio of 20% air / 20% nitrogen / 10% carbon dioxide / 50% water vapor, and finally baked at 40% nitrogen / 10% The active catalyst was o...
PUM
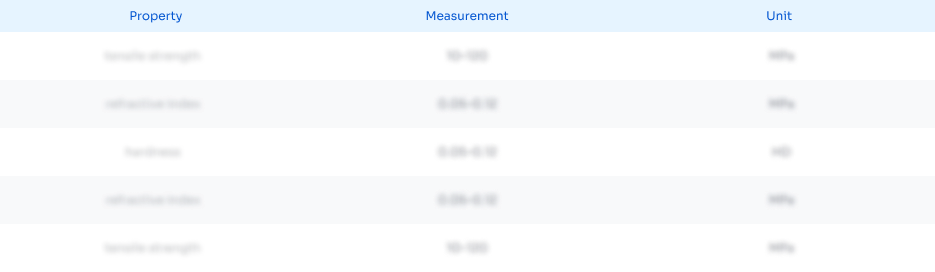
Abstract
Description
Claims
Application Information

- R&D
- Intellectual Property
- Life Sciences
- Materials
- Tech Scout
- Unparalleled Data Quality
- Higher Quality Content
- 60% Fewer Hallucinations
Browse by: Latest US Patents, China's latest patents, Technical Efficacy Thesaurus, Application Domain, Technology Topic, Popular Technical Reports.
© 2025 PatSnap. All rights reserved.Legal|Privacy policy|Modern Slavery Act Transparency Statement|Sitemap|About US| Contact US: help@patsnap.com