High temperature resistant and wear resistant ultrahigh voltage insulation coating and preparation method thereof
An insulating coating and ultra-high voltage technology, applied in the direction of anti-corrosion coatings, coatings, etc., can solve the problems of uneven performance of insulating coatings, unsatisfactory insulation heat resistance, and unsatisfactory insulation performance, so as to improve adhesion and Mechanical strength, shorten grinding time, increase decorative effect
- Summary
- Abstract
- Description
- Claims
- Application Information
AI Technical Summary
Problems solved by technology
Method used
Image
Examples
Embodiment 1
[0031] A high-temperature and wear-resistant ultra-high-voltage insulating coating, comprising: 42 parts by weight of silicone resin, 0.24 parts by weight of aluminate coupling agent, 3 parts of titanium dioxide, 7 parts of quartz sand, and natural camphor : 1 part, nano inorganic filler: 18 parts, solvent: 40 parts, blocked water-based cycloaliphatic polyisocyanate WB-903 curing agent: 0.3 parts, acrylate L-189 leveling agent: 1.4 parts, polyolefin wax anti-settling Agent: 2 parts, anionic polyacrylic acid sodium salt solution HDFSJ-01 dispersant: 0.12 parts, N-369 preservative: 0.1 part and NXZ defoamer: 0.2 parts.
[0032] The mixing weight ratio of nano-silicon nitride powder, nano-silicon carbide powder and nano-magnesia powder in the nano-inorganic filler is 3:1.5:1.
[0033] Its preparation method is:
[0034] 1) Dissolve 0.24 parts by weight of aluminate coupling agent in 4.8 parts by weight of a solvent mixed with hexamethyldisiloxane and xylene at a volume ratio of ...
Embodiment 2
[0038] A high-temperature and abrasion-resistant ultra-high-voltage insulating coating, comprising: 50 parts by weight of silicone resin, 0.62 parts by weight of aluminate coupling agent, 6 parts of titanium dioxide, 10 parts of quartz sand, and natural camphor : 5 parts, nano inorganic filler: 23 parts, solvent: 55 parts, blocked water-based cycloaliphatic polyisocyanate WB-903 curing agent: 0.7 parts, acrylate L-189 leveling agent: 3 parts, polyolefin wax anti-settling Agent: 4 parts, anionic polyacrylic acid sodium salt solution HDFSJ-01 dispersant: 2 parts, N-369 preservative: 0.5 part and NXZ defoamer: 0.5 part.
[0039] The mixing weight ratio of nano-silicon nitride powder, nano-silicon carbide powder and nano-magnesia powder in the nano-inorganic filler is 4:2:1.
[0040] Its preparation method is:
[0041] 1) Dissolve 0.62 parts by weight of aluminate coupling agent in 6 parts by weight of a solvent mixed with hexamethyldisiloxane and xylene at a volume ratio of 2.5:...
Embodiment 3
[0045] A high-temperature-resistant and wear-resistant ultra-high-voltage insulating coating, comprising: 45 parts by weight of silicone resin, 0.5 parts by weight of aluminate coupling agent, 5 parts of titanium dioxide, 8 parts of quartz sand, and natural camphor : 4 parts, nano inorganic filler: 20 parts, solvent: 50 parts, blocked water-based cycloaliphatic polyisocyanate WB-903 curing agent: 0.5 parts, acrylate L-189 leveling agent: 2 parts, polyolefin wax anti-settling Agent: 4 parts, anionic polyacrylic acid sodium salt solution HDFSJ-01 dispersant: 1.6 parts, N-369 preservative: 0.4 parts and NXZ defoamer: 0.4 parts.
[0046] The mixing weight ratio of nano-silicon nitride powder, nano-silicon carbide powder and nano-magnesia powder in the nano-inorganic filler is 3:2.5:1.
[0047] Its preparation method is:
[0048] 1) Dissolve 0.5 parts by weight of aluminate coupling agent in 7 parts by weight of a solvent mixed with hexamethyldisiloxane and xylene at a volume rati...
PUM
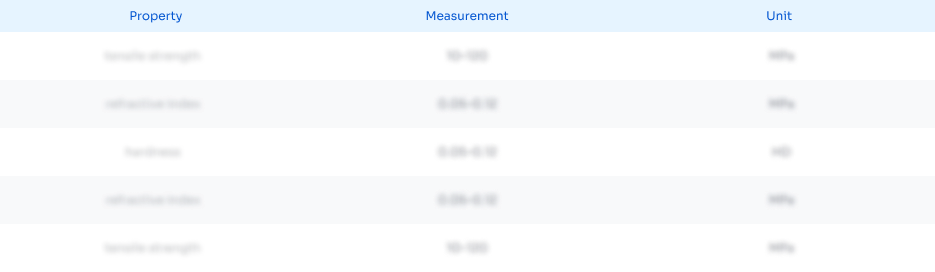
Abstract
Description
Claims
Application Information

- R&D
- Intellectual Property
- Life Sciences
- Materials
- Tech Scout
- Unparalleled Data Quality
- Higher Quality Content
- 60% Fewer Hallucinations
Browse by: Latest US Patents, China's latest patents, Technical Efficacy Thesaurus, Application Domain, Technology Topic, Popular Technical Reports.
© 2025 PatSnap. All rights reserved.Legal|Privacy policy|Modern Slavery Act Transparency Statement|Sitemap|About US| Contact US: help@patsnap.com