Metal-organic framework membrane and preparation method thereof
A metal organic framework and metal source technology, applied in the field of applied chemistry, can solve the problems of easy occurrence of membrane defects, long production cycle, long reaction time, etc., and achieve the effects of batch production and high purity, fast production and simple operation.
- Summary
- Abstract
- Description
- Claims
- Application Information
AI Technical Summary
Problems solved by technology
Method used
Image
Examples
Embodiment 1
[0053] Mix metal source (anhydrous zinc acetate) with organic ligand (2-methylimidazole) and additive (polyethylene glycol, molecular weight 4000). Wherein, relative to 1 mol of organic ligand, the amount of metal source used is 0.1 mol, and the amount of polyethylene glycol used is 0.005 mol. Spread evenly on the base copper foil (4cm*4cm), hot press. The hot-pressing temperature was 220 °C, the hot-pressing pressure was 0.2 MPa, and the hot-pressing time was 25 min. The metal-organic framework material is obtained on the base copper foil, and the metal-organic framework film is prepared.
[0054] The above materials were washed repeatedly with ethanol and dimethylformamide, and dried to obtain a purified metal-organic framework membrane. The metal-organic framework material loading on the film was 10.37 g / m2. In order to carry out X-ray powder diffraction and scanning electron microscope analysis on the metal organic framework film, wherein, X-ray powder diffraction model...
Embodiment 2
[0056] Mix metal source (zinc nitrate hexahydrate) with organic ligand (2-aminoterephthalic acid) and additive (polyvinyl alcohol, molecular weight 16000) evenly. Among them, relative to 1 mol of organic ligand, the amount of metal source is 1 mol, and the amount of polyvinyl alcohol is 0.001 mol. Spread it evenly on the base nickel foam (4cm*4cm), and heat press. The hot-pressing temperature was 85 ℃, the hot-pressing pressure was 0.2 MPa, and the hot-pressing time was 120 min. The metal-organic framework material is obtained on the base foamed nickel, and the metal-organic framework film is prepared.
[0057] The above materials were washed repeatedly with ethanol and dimethylformamide, and dried to obtain a purified metal-organic framework membrane. The MOF loading on the film was 6.03 g / m2. Carry out X-ray powder diffraction and scanning electron microscope analysis on the metal organic framework film, wherein, X-ray powder diffraction model: Bruker D8 Advance, test int...
Embodiment 3
[0059] Mix metal source (cobalt nitrate hexahydrate) with organic ligand (benzimidazole) and additive (polyvinylpyrrolidone, molecular weight 40000) evenly. Among them, relative to 1 mol of organic ligand, the amount of metal source used is 0.01 mol, and the amount of polyvinylpyrrolidone used is 0.002 mol. Evenly spread on the base carbon cloth (4cm*4cm), hot press. The hot-pressing temperature was 120 °C, the hot-pressing pressure was 0.2 MPa, and the hot-pressing time was 70 min. The metal-organic framework material is obtained on the base carbon cloth, and the metal-organic framework film is prepared.
[0060] The above materials were washed repeatedly with ethanol and dimethylformamide, and dried to obtain a purified metal-organic framework membrane. The MOF loading on the membrane was 8.06 g / m2. Carry out X-ray powder diffraction and scanning electron microscope analysis on the metal organic framework film, wherein, X-ray powder diffraction model: Bruker D8 Advance, t...
PUM
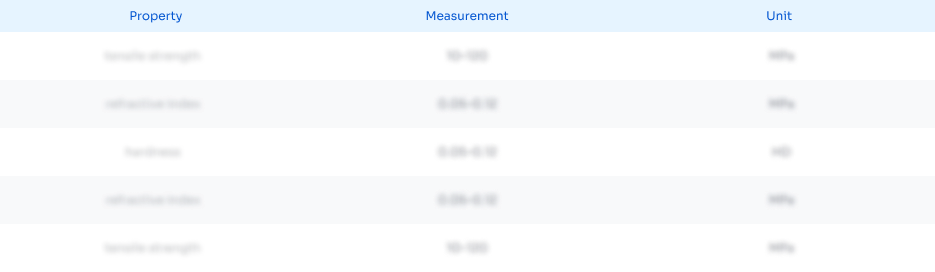
Abstract
Description
Claims
Application Information

- Generate Ideas
- Intellectual Property
- Life Sciences
- Materials
- Tech Scout
- Unparalleled Data Quality
- Higher Quality Content
- 60% Fewer Hallucinations
Browse by: Latest US Patents, China's latest patents, Technical Efficacy Thesaurus, Application Domain, Technology Topic, Popular Technical Reports.
© 2025 PatSnap. All rights reserved.Legal|Privacy policy|Modern Slavery Act Transparency Statement|Sitemap|About US| Contact US: help@patsnap.com