Manufacturing process method of aluminum alloy chassis end of standard EMU
A technology for EMUs and aluminum alloys, applied in manufacturing tools, vehicle parts, metal processing, etc., can solve the problem that the flatness and size of the front plate at the end of the chassis are difficult to control, affect the overall size and welding of the chassis, and cannot guarantee the overall size Requirements and other issues to achieve the effect of improving the overall welding quality and production efficiency, improving the overall welding quality, and improving welding accessibility
- Summary
- Abstract
- Description
- Claims
- Application Information
AI Technical Summary
Problems solved by technology
Method used
Image
Examples
Embodiment Construction
[0032] Material inspection: check the surface quality of the material, oil stains, burrs are not allowed, bumps and scratches are not allowed to exceed 0.1 times the thickness of the plate, and the maximum does not exceed 0.5mm; according to the production order, compare the length and width dimensions of the material with reference to the drawings , Socket form, thickness dimension, flatness, etc. shall be inspected.
[0033] Grinding and cleaning: Lift the parts to the grinding stand or platform, and use dry cotton cloth to remove the dust on the surface of the profile and parts. Use a straight handle grinder to grind the weld area, the grinding area is 15-25mm, and the grinding is required until the metallic luster is exposed.
[0034] refer to figure 1 , optimize the aluminum structure at the end of the underframe, and divide the overall structure of the end of the underframe into end beam traction beam synthesis 1, end beam front plate 2, end beam bottom plate 3, and und...
PUM
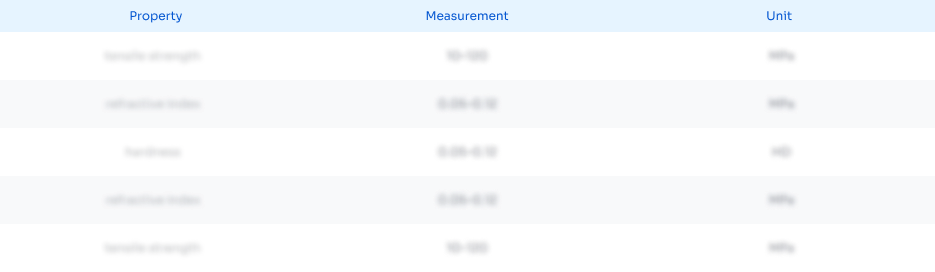
Abstract
Description
Claims
Application Information

- Generate Ideas
- Intellectual Property
- Life Sciences
- Materials
- Tech Scout
- Unparalleled Data Quality
- Higher Quality Content
- 60% Fewer Hallucinations
Browse by: Latest US Patents, China's latest patents, Technical Efficacy Thesaurus, Application Domain, Technology Topic, Popular Technical Reports.
© 2025 PatSnap. All rights reserved.Legal|Privacy policy|Modern Slavery Act Transparency Statement|Sitemap|About US| Contact US: help@patsnap.com