Method for preparing nanometer tungsten carbide-cobalt hard alloy material
A nano-tungsten carbide and cemented carbide technology, which is applied in the field of alloy materials, can solve the problems of low electrical conductivity and low strength, and achieve the effects of high density, long service life and strong cutting ability.
- Summary
- Abstract
- Description
- Claims
- Application Information
AI Technical Summary
Problems solved by technology
Method used
Examples
preparation example Construction
[0014] A preparation method of nanometer tungsten carbide-cobalt hard alloy material, raw material percentage by weight: 50-100nm tungsten carbide nanopowder 30%, 70-100nm cobalt nanopowder 65%, dehydrated alcohol 5%;
[0015] The preparation steps are:
[0016] a. The tungsten carbide nano-powder and the cobalt nano-powder are mixed by ball milling in absolute ethanol medium, the ball milling speed is controlled to 150r / min, and the mixing time is 3 hours;
[0017] b. Granulation;
[0018] c. Drying, the mixture powder is dried at 50-70°C for 2 hours;
[0019] d. Vacuum sintering, the sintering temperature is 1300°C, and the sintering time is 5s.
specific Embodiment approach 2
[0020] A preparation method of nanometer tungsten carbide-cobalt hard alloy material, raw material percentage by weight: 50-100nm tungsten carbide nanopowder 80%, 70-100nm cobalt nanopowder 17%, dehydrated alcohol 3%;
[0021] The preparation steps are:
[0022] a. The tungsten carbide nanopowder and the cobalt nanopowder are ball milled and mixed in an anhydrous ethanol medium, the ball milling speed is controlled to 170r / min, and the mixing time is 2 hours;
[0023] b. Granulation;
[0024] c, drying, the mixture powder is dried at 50-70°C for 3 hours;
[0025] d. Vacuum sintering, the sintering temperature is 1380°C, and the time is 3s.
specific Embodiment approach 3
[0026] A preparation method of nanometer tungsten carbide-cobalt hard alloy material, raw material percentage by weight: 50-100nm tungsten carbide nanopowder 60%, 70-100nm cobalt nanopowder 33%, dehydrated alcohol 7%;
[0027] The preparation steps are:
[0028] a. The tungsten carbide nanopowder and the cobalt nanopowder are mixed by ball milling in an anhydrous ethanol medium, the ball milling speed is controlled to 130r / min, and the mixing time is 4 hours;
[0029] b. Granulation;
[0030] c, drying, the mixture powder is dried at 50-70°C for 3 hours;
[0031] d. Vacuum sintering, the sintering temperature is 1500°C, and the sintering time is 1s.
PUM
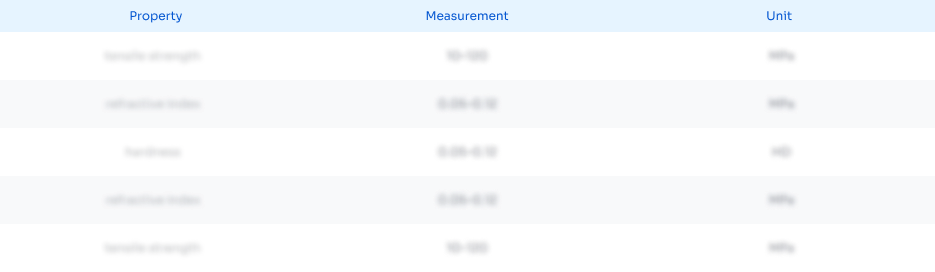
Abstract
Description
Claims
Application Information

- Generate Ideas
- Intellectual Property
- Life Sciences
- Materials
- Tech Scout
- Unparalleled Data Quality
- Higher Quality Content
- 60% Fewer Hallucinations
Browse by: Latest US Patents, China's latest patents, Technical Efficacy Thesaurus, Application Domain, Technology Topic, Popular Technical Reports.
© 2025 PatSnap. All rights reserved.Legal|Privacy policy|Modern Slavery Act Transparency Statement|Sitemap|About US| Contact US: help@patsnap.com