Method for extracting oil in spent bleaching clay by ultrasonic assisted isohexane
An ultrasonic-assisted, isohexane technology is applied in the direction of recycling fat oil/fatty acid from waste materials, producing fat, and recycling fatty substances. It can solve problems such as low oil yield, expensive mechanical equipment, and hidden dangers in production and life, and reduce Effects of production cost, increase of industrial profit, and shortening of production time
- Summary
- Abstract
- Description
- Claims
- Application Information
AI Technical Summary
Problems solved by technology
Method used
Examples
specific Embodiment approach 1
[0009] Specific embodiment 1: The method for extracting grease from waste clay with ultrasonic-assisted isohexane is realized through the following steps: 1. Take a certain amount of grease decolorization waste white, and mix it with a certain amount of isohexane evenly for a period of time; 2. Use 1 : 4 to 1:8 (w:v) ratio of solid to liquid, when the ultrasonic temperature is 45-65°C, use ultrasonic power 200-400W, ultrasonic extraction time is 20-40min; 3. Centrifuge the obtained mixture Filtration treatment, the supernatant liquid is the extracted oil, and the residue obtained by filtration is the waste clay after oil extraction; 4. The obtained deoiled waste clay is washed with a certain amount of water to remove isohexane, and it is washed three times in total, and dried after washing for further use. Five, the isohexane solvent in the leaching solution is recovered.
specific Embodiment approach 2
[0010] Embodiment 2: The difference between this embodiment and Embodiment 1 is that the ratio of material to liquid in Step 2 is 1:5-1:7. Other steps are the same as in the first embodiment.
specific Embodiment approach 3
[0011] Embodiment 3: The difference between this embodiment and Embodiment 1 is that the ultrasonic temperature in step 2 is 50-60°C. Other steps are the same as in the first embodiment.
PUM
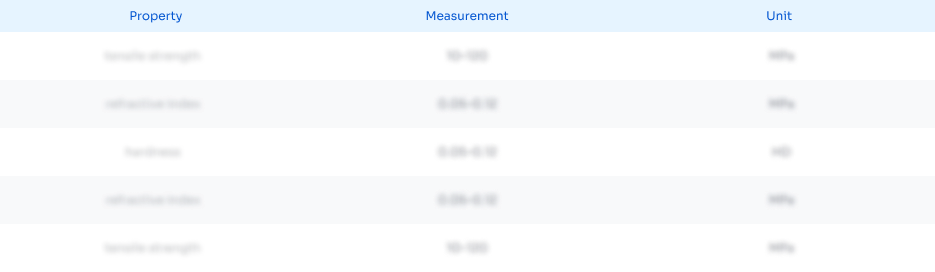
Abstract
Description
Claims
Application Information

- R&D
- Intellectual Property
- Life Sciences
- Materials
- Tech Scout
- Unparalleled Data Quality
- Higher Quality Content
- 60% Fewer Hallucinations
Browse by: Latest US Patents, China's latest patents, Technical Efficacy Thesaurus, Application Domain, Technology Topic, Popular Technical Reports.
© 2025 PatSnap. All rights reserved.Legal|Privacy policy|Modern Slavery Act Transparency Statement|Sitemap|About US| Contact US: help@patsnap.com