Bottom pouring system
A pouring system and bottom-injection technology, used in casting molding equipment, molds, cores, etc., can solve the problems of easy fracture of ceramic cores, premature solidification of the selection end before crystal pulling, and insufficient slag filtration. Simple structure, improved grain orientation pass rate, and easy assembly
- Summary
- Abstract
- Description
- Claims
- Application Information
AI Technical Summary
Problems solved by technology
Method used
Image
Examples
Embodiment Construction
[0028] The embodiments of the present invention will be described in detail below with reference to the accompanying drawings, but the present invention can be implemented in many different ways defined and covered by the claims.
[0029] like image 3 As shown, the preferred embodiment of the present invention provides a bottom pouring gating system, comprising a disc runner 1, the disc runner 1 includes a disc main sprue 11 for the pouring liquid to pass through, and the disc main sprue 11 The upper end of the first filter screen 2 is connected with the first filter screen 2 for filtering the pouring liquid, and the upper end of the first filter screen 2 is connected with the sprue cup 3 for introducing the pouring liquid; the lower end of the disc main pouring pipe 11 is connected with a vertical center column Runner 4, the bottom end of the center column runner 4 is connected with the bottom pouring runner 5; the disc runner 1 is connected with the blade 6, and the bottom ...
PUM
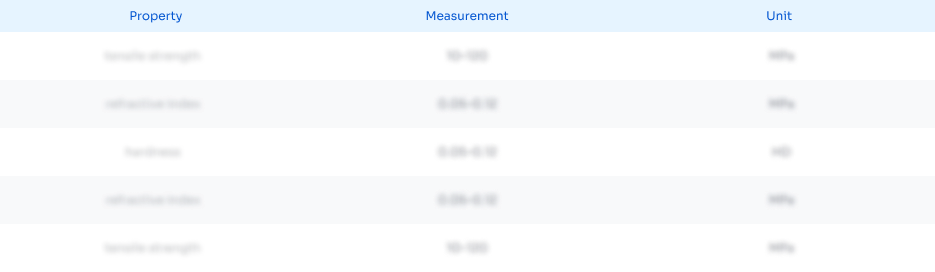
Abstract
Description
Claims
Application Information

- Generate Ideas
- Intellectual Property
- Life Sciences
- Materials
- Tech Scout
- Unparalleled Data Quality
- Higher Quality Content
- 60% Fewer Hallucinations
Browse by: Latest US Patents, China's latest patents, Technical Efficacy Thesaurus, Application Domain, Technology Topic, Popular Technical Reports.
© 2025 PatSnap. All rights reserved.Legal|Privacy policy|Modern Slavery Act Transparency Statement|Sitemap|About US| Contact US: help@patsnap.com