Gear fault detection method on the basis of multi-position turning angle signals of encoders
A technology for angle signal and fault detection, applied in the direction of machine gear/transmission mechanism testing, etc., can solve the problems of low amount of running shaft information, limited diagnostic analysis, complex frequency components, etc., to improve the fault recognition rate, easy installation, and resolution. high effect
- Summary
- Abstract
- Description
- Claims
- Application Information
AI Technical Summary
Problems solved by technology
Method used
Image
Examples
Embodiment Construction
[0037] specific implementation plan
[0038] The present invention is described in detail below in conjunction with accompanying drawing:
[0039] refer to figure 1 , a gear broken tooth fault identification method based on encoder multi-bit rotation angle signals, comprising the following steps:
[0040] 1) Install a shaft angle encoder to extract the operating status signal of the gearbox system e. There are two installation methods. One is to install encoders c and d on the input shaft a and output shaft b of the gearbox respectively, which is called double The shaft encoder information acquisition method; the second is to only install the encoder d on the output shaft b of the gearbox, which is called the output single-axis encoder information acquisition method;
[0041] 2) Collect the shaft angle encoder rotation angle signal x of the gearbox system (including spur gearboxes, helical gearboxes, planetary gear reducers, etc.) i (n), n is the number of sampling points, ...
PUM
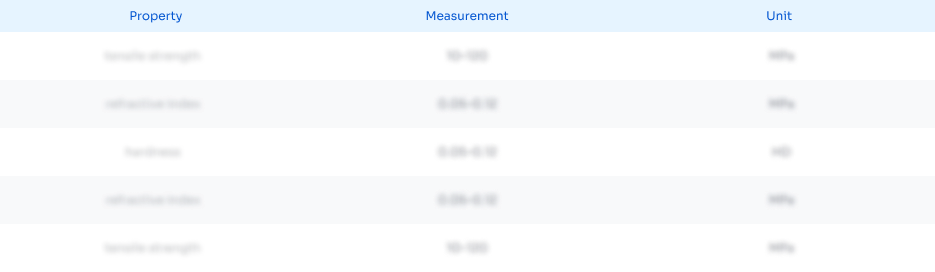
Abstract
Description
Claims
Application Information

- Generate Ideas
- Intellectual Property
- Life Sciences
- Materials
- Tech Scout
- Unparalleled Data Quality
- Higher Quality Content
- 60% Fewer Hallucinations
Browse by: Latest US Patents, China's latest patents, Technical Efficacy Thesaurus, Application Domain, Technology Topic, Popular Technical Reports.
© 2025 PatSnap. All rights reserved.Legal|Privacy policy|Modern Slavery Act Transparency Statement|Sitemap|About US| Contact US: help@patsnap.com