Method for increasing yield of xylene by transalkylation of aromatic hydrocarbon and cracking of non-aromatic hydrocarbon
A technology for aromatic alkyl and non-aromatic hydrocarbons, which is applied in the fields of hydrocarbon cracking to produce hydrocarbons, chemical instruments and methods, and bulk chemical production, etc.
- Summary
- Abstract
- Description
- Claims
- Application Information
AI Technical Summary
Problems solved by technology
Method used
Image
Examples
Embodiment 1
[0013] Na 2 O content less than 0.1% (weight), SiO 2 / Al 2 o 3 66.7 grams of ZSM-5 molecular sieve with a molecular ratio of 50 and Na 2 γ-Al with O content less than 0.1% by weight 2 o 3 ·H 2 O57.1 g was evenly mixed, then added a certain amount of dilute nitric acid and Tianqing powder, kneaded evenly, extruded, dried at 120°C for 4 hours, and roasted at 500°C for 3 hours to obtain catalyst A1
[0014] SiO 2 / Al 2 o 3 Beta zeolite 60.0 g with a molecular ratio of 50 and Na 2 γ-Al with O content less than 0.1% by weight 2 o 3 ·H 2 O57.1 g is evenly mixed, then a certain amount of dilute nitric acid and Tianqing powder are added and kneaded evenly, extruded into strips, roasted to make a carrier, and placed in an impregnation container after pelletizing. A certain amount of ammonium perrhenate was dissolved in water, impregnated on the surface of the carrier, dried at 120°C for 4 hours, and calcined at 500°C for 3 hours to obtain catalyst B1.
[0015] In the fixe...
Embodiment 2
[0017] Na 2 O content less than 0.1% (weight), SiO 2 / Al 2 o 3 66.7 grams of Beta molecular sieve with a molecular ratio of 50 and Na 2 γ-Al with O content less than 0.1% by weight 2 o 3 ·H 2 O57.1 g was uniformly mixed, then added a certain amount of dilute nitric acid and Tianqing powder, kneaded evenly, extruded, roasted to make a carrier, dried at 120 ° C for 4 hours, and roasted at 500 ° C for 3 hours to obtain catalyst A2.
[0018] Na 2 O content less than 0.1% (weight), SiO 2 / Al 2 o 3 66.7 grams of ZSM-12 molecular sieve with a molecular ratio of 60 and Na 2 γ-Al with O content less than 0.1% by weight 2 o 3 ·H 2 O57.1 g was uniformly mixed, then added a certain amount of dilute nitric acid and ammonium molybdate aqueous solution, kneaded evenly, extruded, and roasted at 550°C to make the second layer of catalyst B2.
[0019] In the fixed-bed reactor, install 10 grams of catalyst A2 in the upper bed, and 10 grams of catalyst B2 in the lower bed, pass in h...
Embodiment 3
[0021] Na 2 O content less than 0.1% (weight), SiO 2 / Al 2 o 3 66.7 grams of Mor molecular sieve with a molecular ratio of 40 and Na 2γ-Al with O content less than 0.1% by weight 2 o 3 ·H 2 O57.1 g is evenly mixed, then a certain amount of dilute nitric acid and Tianqing powder are added and kneaded evenly, extruded into strips, roasted to make a carrier, and placed in an impregnation container after pelletizing. A certain amount of ammonium molybdate was dissolved in an appropriate amount of water, impregnated on the surface of the carrier, dried at 120°C for 4 hours, and calcined at 500°C for 3 hours to prepare the first layer of catalyst A3.
[0022] Na 2 O content less than 0.1% (weight), SiO 2 / Al 2 o 3 46 grams of Mor molecular sieve with a molecular ratio of 80, Na 2 O content less than 0.1% (weight), SiO 2 / Al 2 o 3 20.7 grams of Beta molecular sieve with a molecular ratio of 60, Na 2 γ-Al with O content less than 0.1% by weight 2 o 3 ·H 2 057.1 grams...
PUM
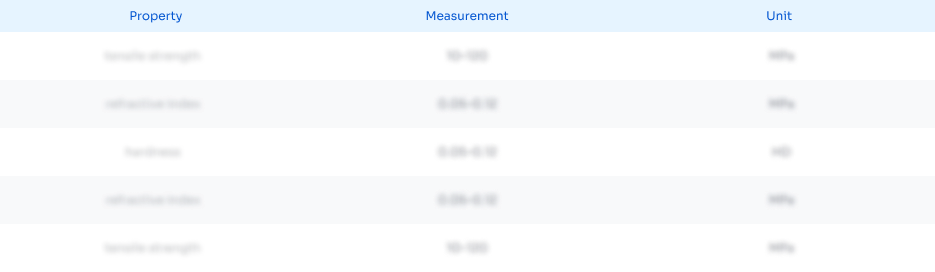
Abstract
Description
Claims
Application Information

- R&D
- Intellectual Property
- Life Sciences
- Materials
- Tech Scout
- Unparalleled Data Quality
- Higher Quality Content
- 60% Fewer Hallucinations
Browse by: Latest US Patents, China's latest patents, Technical Efficacy Thesaurus, Application Domain, Technology Topic, Popular Technical Reports.
© 2025 PatSnap. All rights reserved.Legal|Privacy policy|Modern Slavery Act Transparency Statement|Sitemap|About US| Contact US: help@patsnap.com