Method for improving polyimide-based carbon fiber microstructure
A polyimide-based carbon fiber, polyimide fiber technology, applied in the field of carbon fiber, can solve the problems of increased production cost, increased production time, fiber defects, etc., and achieves low cost, reduced adverse effects, and high carbon content. Effect
- Summary
- Abstract
- Description
- Claims
- Application Information
AI Technical Summary
Problems solved by technology
Method used
Image
Examples
Embodiment 1
[0034] A: BPDA and ODA were mechanically stirred in DMAc at low temperature for a certain period of time to obtain a BPDA / ODA polyamic acid solution.
[0035]B: The polyamic acid fiber is prepared by wet spinning process, and the temperature of the polyamic acid fiber is raised gradually, and the thermal imidization treatment is carried out to obtain the polyimide fiber;
[0036] C: Fix the raw silk in a vacuum tube furnace, set a gradient temperature rise program, heat from room temperature to 1500°C at a heating rate of 10°C / min and keep it at this temperature for 70 minutes, and pass through nitrogen protection, and the flow rate is 300-400ml / min, carry out carbonization treatment, and cool naturally after the end to obtain polyimide-based carbon fibers.
Embodiment 2
[0038] A: BPDA, ODA and p-PDA are mechanically stirred in DMAc at low temperature for a certain period of time to obtain BPDA / ODA / p-PDA30% (the percentage represents the mole percentage of p-PDA monomer in diamine) Copolymerized polyamic acid solution.
[0039] B: The polyamic acid fiber is prepared by wet spinning process, and the temperature of the polyamic acid fiber is raised gradually, and the thermal imidization treatment is carried out to obtain the polyimide fiber;
[0040] C: Fix the raw silk in a vacuum tube furnace, set a gradient temperature rise program, heat from room temperature to 1500°C at a heating rate of 10°C / min and keep it at this temperature for 70 minutes, and pass through nitrogen protection, and the flow rate is 300-400ml / min, carry out carbonization treatment, and cool naturally after the end to obtain polyimide-based carbon fibers.
Embodiment 3
[0042] A: BPDA, ODA and p-PDA were mechanically stirred in DMAc at low temperature for a certain period of time to prepare a 50% BPDA / ODA / p-PDA copolymerized polyamic acid solution.
[0043] B: The polyamic acid fiber is prepared by wet spinning process, and the temperature of the polyamic acid fiber is raised gradually, and the thermal imidization treatment is carried out to obtain the polyimide fiber;
[0044] C: Fix the raw silk in a vacuum tube furnace, set a gradient temperature rise program, heat from room temperature to 1500°C at a heating rate of 10°C / min and keep it at this temperature for 70 minutes, and pass through nitrogen protection, and the flow rate is 300-400ml / min, carry out carbonization treatment, and cool naturally after the end to obtain polyimide-based carbon fibers.
PUM
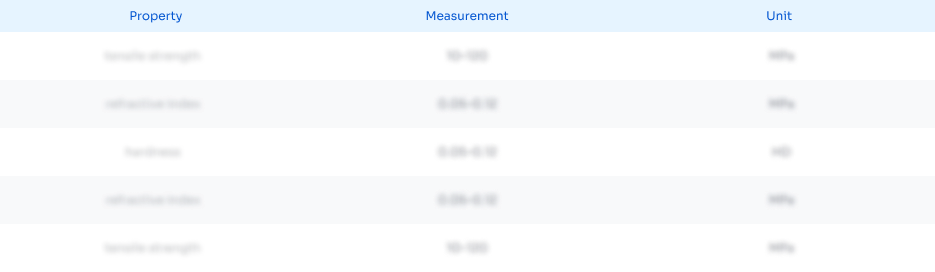
Abstract
Description
Claims
Application Information

- R&D
- Intellectual Property
- Life Sciences
- Materials
- Tech Scout
- Unparalleled Data Quality
- Higher Quality Content
- 60% Fewer Hallucinations
Browse by: Latest US Patents, China's latest patents, Technical Efficacy Thesaurus, Application Domain, Technology Topic, Popular Technical Reports.
© 2025 PatSnap. All rights reserved.Legal|Privacy policy|Modern Slavery Act Transparency Statement|Sitemap|About US| Contact US: help@patsnap.com