High-reliability installation method for high-voltage welding spots
A high-pressure welding and high-spot technology, which is applied in welding equipment, metal processing, metal processing equipment, etc., can solve the problems of satellite power supply and distribution subsystem failure, unsatisfactory long-term use, low-pressure discharge solder joints, etc., to prevent The effect of low pressure discharge phenomenon, round surface and reliable electrical connection
- Summary
- Abstract
- Description
- Claims
- Application Information
AI Technical Summary
Problems solved by technology
Method used
Image
Examples
Embodiment 1
[0049] Step (1), forming and cutting the plug-in resistor pins, the length of the pins protruding from the soldering surface of the printed board is 0.5mm; tinning the cut pins, and tinning the plug-in resistors Resistor pins mounted into soldered through-holes on the printed board;
[0050] Step (2), first solder the plug-in resistor pins installed on the printed board:
[0051] Use a smart electric soldering iron to solder the pins for the first time, and the temperature of the soldering iron tip is 320°C. Welding time is 3s. When soldering, use one side (welding surface) welding method, that is, the solder flows from the welding surface to the component surface; after the first welding, the qualified plug-in pins and printed board solder joints refer to figure 2 shown;
[0052] For the first cleaning of the solder joints after the first soldering, manual cleaning is used, that is, the solder joints after the first soldering are repeatedly scrubbed with dust-free paper d...
PUM
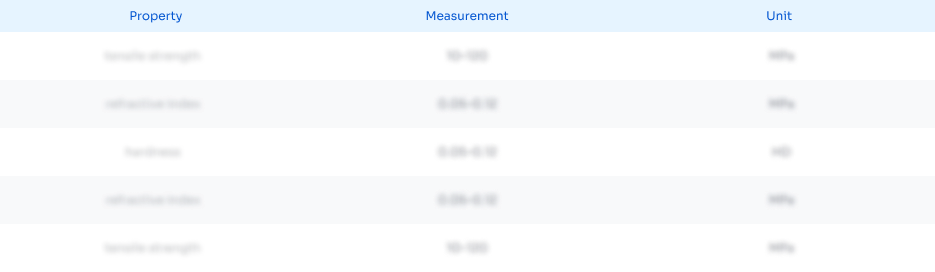
Abstract
Description
Claims
Application Information

- Generate Ideas
- Intellectual Property
- Life Sciences
- Materials
- Tech Scout
- Unparalleled Data Quality
- Higher Quality Content
- 60% Fewer Hallucinations
Browse by: Latest US Patents, China's latest patents, Technical Efficacy Thesaurus, Application Domain, Technology Topic, Popular Technical Reports.
© 2025 PatSnap. All rights reserved.Legal|Privacy policy|Modern Slavery Act Transparency Statement|Sitemap|About US| Contact US: help@patsnap.com