Dry method for manufacturing fiber board through cow dung
A fiberboard and cow dung technology, applied in applications, household components, flat products, etc., can solve the problems of high cost of fiberboard, unfavorable environmental protection, etc., and achieve the effect of simple preparation method, waste recycling and low cost
- Summary
- Abstract
- Description
- Claims
- Application Information
AI Technical Summary
Problems solved by technology
Method used
Image
Examples
Embodiment 1
[0014] Embodiment 1: a kind of method for preparing fiberboard with cow dung dry method, comprises the steps:
[0015] Step1, wash 5 times with distilled water and 15g of cow dung after cleaning with bamboo vinegar; then filter, dry, pulverize and sieve to obtain 1mm fiber;
[0016] Step2. Dissolve the NaOH solid in distilled water, stir the prepared solution and fiber evenly at room temperature, and then put it into a drying oven for activation. The activation temperature is 150°C for 30 minutes; the mass ratio of NaOH solid to distilled water is 1:1;
[0017] Step3. After adding MDI ecological glue to the fiber obtained in Step2; put it into a high-speed mixer and mix it, condition: 140r / min for 7min; then add paraffin emulsion and stir, condition: 140r / min for 16min; then dry it to make it contain water The rate is 7%; wherein, MDI ecological glue accounts for 6% of the mixture quality of fiber and MDI ecological glue, and paraffin emulsion accounts for 1% of the mixture qu...
Embodiment 2
[0023] Embodiment 2: a kind of method for preparing fiberboard with cow dung dry method, comprises the steps:
[0024] Step1, wash 6 times with distilled water Cow manure 15g after cleaning with bamboo vinegar liquid; Then filter, dry, pulverize and sieve to obtain the fiber of 5mm;
[0025] Step2. Dissolve the NaOH solid in distilled water, stir the prepared solution and fiber evenly at room temperature, and then put it into a drying oven for activation. The activation temperature is 150°C for 30 minutes; the mass ratio of NaOH solid to distilled water is 1:1;
[0026] Step3, Step3, after adding MDI ecological glue to the fiber obtained in Step2; put it into a high-speed mixer and mix it, condition: 140r / min for 7min; then add paraffin emulsion and stir, condition: 140r / min for 16min; then dry it Its water content is 12%; Among them, MDI ecological glue accounts for 10% of the mixture quality that fiber and MDI ecological glue forms, and paraffin emulsion accounts for 2% of t...
Embodiment 3
[0032] Embodiment 3: a kind of method for preparing fiberboard with cow dung dry method, comprises the steps:
[0033] Step1, wash 6 times with distilled water and 15g of cow dung after cleaning with bamboo vinegar; then filter, dry, pulverize and screen to obtain 3mm fiber;
[0034] Step2. Dissolve the NaOH solid in distilled water, stir the prepared solution and fiber evenly at room temperature, and then put it into a drying oven for activation. The activation temperature is 150°C for 30 minutes; the mass ratio of NaOH solid to distilled water is 1:1;
[0035] Step3. After adding MDI ecological glue to the fiber obtained in Step2; put it into a high-speed mixer and mix it, condition: 140r / min for 7min; then add paraffin and stir, condition: 140r / min for 16min; then dry it to make the moisture content 10%; wherein, MDI ecological glue accounts for 7% of the mixture quality of fiber and MDI ecological glue, and paraffin accounts for 1.5% of the mixture quality of fiber, MDI ec...
PUM
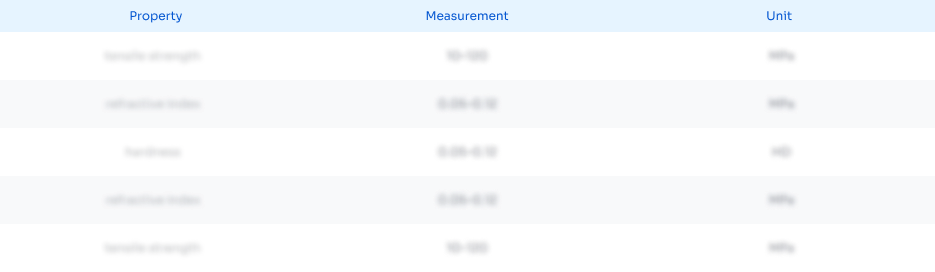
Abstract
Description
Claims
Application Information

- R&D
- Intellectual Property
- Life Sciences
- Materials
- Tech Scout
- Unparalleled Data Quality
- Higher Quality Content
- 60% Fewer Hallucinations
Browse by: Latest US Patents, China's latest patents, Technical Efficacy Thesaurus, Application Domain, Technology Topic, Popular Technical Reports.
© 2025 PatSnap. All rights reserved.Legal|Privacy policy|Modern Slavery Act Transparency Statement|Sitemap|About US| Contact US: help@patsnap.com