Liquid material filling control device and method
A liquid material and control device technology, applied in liquid bottling, liquid processing, packaging, etc., can solve the problems of irregular fluctuation of the flow of the filling head, difficult to clean, and low filling speed, and simplify the filling process. , Reduce material waste, improve speed and accuracy
- Summary
- Abstract
- Description
- Claims
- Application Information
AI Technical Summary
Problems solved by technology
Method used
Image
Examples
Embodiment Construction
[0017] The present invention will be further described below in conjunction with the accompanying drawings and embodiments.
[0018] At present, liquid quantitative filling equipment, in order to meet the dual requirements of filling speed and filling accuracy, mostly adopts the double-speed filling mode: firstly, high-speed filling with large flow rate is used, and the large flow rate is turned off when the filling volume reaches the required filling volume. Filling, switch to small flow filling to meet the requirements of high speed and high precision. Therefore, the idea of the present invention is: in combination with the characteristics of the above method, when the filling equipment is filling at a large flow rate, it uses pressure filling to increase the filling speed, and when filling at a small flow rate, it is converted to self-flow filling or Stable pressure filling similar to gravity filling to ensure filling accuracy.
[0019] Such as figure 1 As shown, the li...
PUM
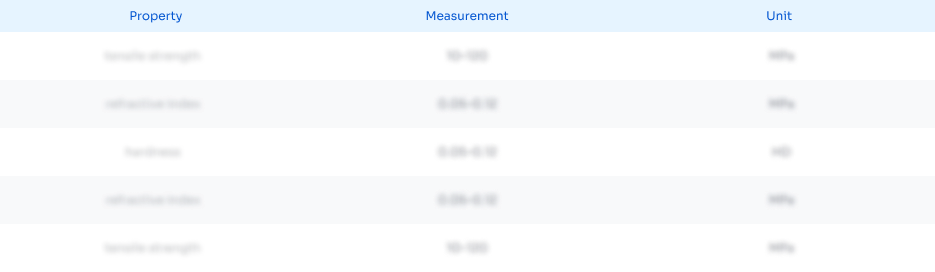
Abstract
Description
Claims
Application Information

- R&D
- Intellectual Property
- Life Sciences
- Materials
- Tech Scout
- Unparalleled Data Quality
- Higher Quality Content
- 60% Fewer Hallucinations
Browse by: Latest US Patents, China's latest patents, Technical Efficacy Thesaurus, Application Domain, Technology Topic, Popular Technical Reports.
© 2025 PatSnap. All rights reserved.Legal|Privacy policy|Modern Slavery Act Transparency Statement|Sitemap|About US| Contact US: help@patsnap.com