Magnetron sputtering method for depositing thin films
A magnetron sputtering and thin film technology, applied in the field of magnetron sputtering, can solve problems such as pressure increase, inability to fill through silicon holes, process failure, etc., and achieve the effects of improving quality, reducing deposition rate and deposition density
- Summary
- Abstract
- Description
- Claims
- Application Information
AI Technical Summary
Problems solved by technology
Method used
Image
Examples
Embodiment 1
[0052] In this embodiment, a Ti film is deposited in the TSV as a barrier layer. In this embodiment, magnetron sputtering equipment is used to deposit the Ti film. In combination with Table 1, the specific deposition steps of this embodiment are described as follows:
[0053] (1) feed argon gas: feed argon gas 7s in the reaction chamber of magnetron sputtering equipment; Control the flow rate of argon gas to be 100 sccm;
[0054] (2) Starting: Turn on the DC power supply, apply a DC bias to the target, and control the power of the DC bias to 1000W; control the starting time to 2s;
[0055] It should be noted that, in this step, the argon gas was continuously fed and the flow rate of 100 sccm was maintained.
[0056] (3) Depressurization: stop the feeding of argon for 2s, reduce the pressure in the reaction chamber;
[0057] (4) Thin film deposition: increase the DC bias voltage of 1000W applied to the target to 38000W, and apply a 600W RF bias voltage on the lower electrode a...
PUM
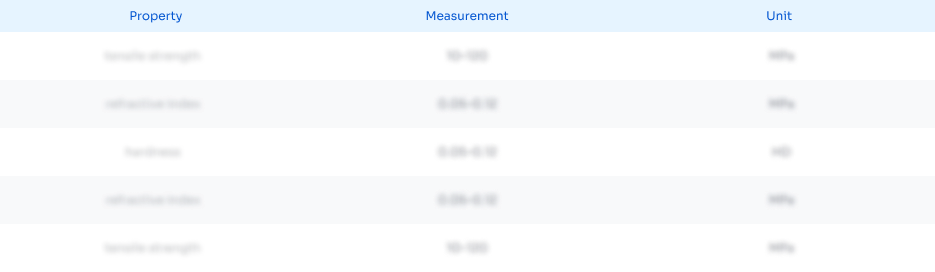
Abstract
Description
Claims
Application Information

- Generate Ideas
- Intellectual Property
- Life Sciences
- Materials
- Tech Scout
- Unparalleled Data Quality
- Higher Quality Content
- 60% Fewer Hallucinations
Browse by: Latest US Patents, China's latest patents, Technical Efficacy Thesaurus, Application Domain, Technology Topic, Popular Technical Reports.
© 2025 PatSnap. All rights reserved.Legal|Privacy policy|Modern Slavery Act Transparency Statement|Sitemap|About US| Contact US: help@patsnap.com