Calcium-aluminum-lead alloy for battery pole plate and preparation method thereof
A battery plate and lead alloy technology, which is applied to battery electrodes, circuits, electrical components, etc., can solve the problems of reducing smelting costs, achieve long storage time, not easy to pulverize, and reduce burning loss
- Summary
- Abstract
- Description
- Claims
- Application Information
AI Technical Summary
Problems solved by technology
Method used
Examples
example 1
[0043] Under the protection of a continuous argon atmosphere, take 2.2kg of pure aluminum ingot, heat it up to 900°C in an induction furnace to melt it, and then add 6.8kg of pure calcium block to it while stirring, and control the temperature of mixed smelting at 930°C. After it is completely melted, continue to stir and add 1.0kg of lead block. The temperature of the mixed smelting is controlled at 950°C, and it is stirred for 8 minutes until the alloy is completely melted. Then, it is cast into an intermediate alloy through a casting device, cooled naturally in the air and made into a finished intermediate alloy. , put into storage after detection and weighing. Its composition and content are: Ca: 68wt%, Al: 22wt%, Pb10wt%.
example 2
[0045] Under the protection of a continuous argon atmosphere, take 2.5kg of pure aluminum ingot, heat it up to 900°C in an induction furnace to melt it, and then add 7.0kg of pure calcium block to it while stirring, and control the temperature of mixed smelting at 950°C. After it is completely melted, continue to stir and add 0.5kg of lead. The temperature of the mixed smelting is controlled at 980°C. Stir for 10 minutes until the alloy is completely melted. Then, it is cast into an intermediate alloy through a casting device, cooled naturally in the air and made into a finished intermediate alloy. , put into storage after detection and weighing. Its composition and content are: Ca: 70wt%, Al: 25wt%, Pb: 5wt%.
example 3
[0047] Under the protection of a continuous argon atmosphere, take 1.0kg of pure aluminum ingot, heat it up to 900°C in an induction furnace to melt it, and then add 8.2kg of pure calcium block to it while stirring, and control the temperature of mixed smelting at 980°C. After it is completely melted, continue to stir and add 0.8kg of lead weight. The temperature of mixing and smelting is controlled at 1000°C. Stir for 8 minutes until the alloy is completely melted. At this time, carry out reverse stirring for 3 minutes. Then it is cast into master alloy by casting device, cooled naturally in the air and made into finished master alloy, which is checked and weighed before storage. Its composition and content are: Ca: 82wt%, Al: 13wt%, Pb: 5wt%.
[0048] Although the three embodiments all use argon as the shielding gas, it is due to the high cost performance of argon. In the case of higher requirements for product accuracy, other inert gases can be selected. In order to coopera...
PUM
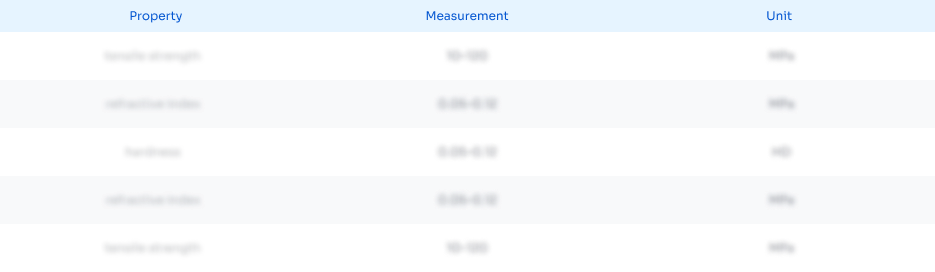
Abstract
Description
Claims
Application Information

- Generate Ideas
- Intellectual Property
- Life Sciences
- Materials
- Tech Scout
- Unparalleled Data Quality
- Higher Quality Content
- 60% Fewer Hallucinations
Browse by: Latest US Patents, China's latest patents, Technical Efficacy Thesaurus, Application Domain, Technology Topic, Popular Technical Reports.
© 2025 PatSnap. All rights reserved.Legal|Privacy policy|Modern Slavery Act Transparency Statement|Sitemap|About US| Contact US: help@patsnap.com