Salt crystallizing processing technology and device for zero discharge of high salt wastewater
A treatment process and technology for salty wastewater, which is applied in water/sewage multi-stage treatment, water/sludge/sewage treatment, chemical industry, etc. It can solve problems such as blockage, production shutdown, and the inability of equipment to operate stably for a long period of time, and achieve high efficiency. High, no secondary pollution, significant economic and social benefits
- Summary
- Abstract
- Description
- Claims
- Application Information
AI Technical Summary
Problems solved by technology
Method used
Image
Examples
Embodiment 1
[0027] Such as figure 1 As shown, a zero-discharge crystalline salt treatment process and device for high-salt wastewater, the process mainly includes pretreatment, evaporation, crystallization, carbonization and other processes, and the treatment process equipment includes at least a degassing tower, an evaporator, a crystallizer, and a carbonization furnace Wait. The high-salt wastewater can be processed through the above-mentioned process to obtain solid crystalline salt, and at the same time, the water can be recovered for factory reuse. The TDS of high-concentration brine in the evaporator is greater than 150,000mg / L; the TDS in the crystallizer is greater than 300,000mg / L, and the crystalline solid SS is 100,000-300,000mg / L; the crystallized salt removes organic matter and nitrate in the carbonization furnace, and the carbonization furnace The temperature is controlled at 600-700°C, the carbonization time is 5-30min, and the tail gas of the carbonization furnace enters ...
Embodiment 2
[0032]The high-salt wastewater is treated with acid and alkali stirring, membrane chemical pretreatment (removing 90% of the saline wastewater), preheating with desalted water, and degassing treatment, and then the wastewater enters the evaporator, using externally provided low-pressure steam (factory Waste steam, exhaust gas waste heat recovery steam or medium pressure steam after decompression and decompression steam), evaporate and crystallize the concentrated brine in the evaporator tube bundle, after evaporation, the TDS (total dissolved solids) in the saline wastewater is 150000mg / L or more, and the separated steam is condensed into clean water and then recycled. After the evaporation process, the salty waste water is crystallized through the crystallizer, wherein the crystallizer is connected to the carbonization furnace, and the heat source of the crystallizer is provided by the high-temperature flue gas heat of the carbonization furnace, and the high-temperature flue ...
Embodiment 3
[0034] In the above two embodiments, the evaporator can be one of forced circulation evaporator, vertical falling film evaporator, and horizontal falling film evaporator, and the evaporation process adopts single-effect or multi-effect evaporation. Use one or a combination of external steam supply, mechanical vapor compression, and thermal vapor compression. The crystallizer adopts one of forced circulation crystallizer, DTB type crystallizer, and OSLO type crystallizer; in the crystallization process, one or a combination of external steam supply, mechanical steam compression, and thermal steam compression is used , and the operating pressure of the crystallizer adopts positive pressure or negative pressure. The flow velocity of the fluid in the heating tube of the crystallizer is 1-3m / s, and the temperature rise of the fluid passing through the heating tube is less than 2°C. The carbonization furnace can be a rotary kiln or a pusher kiln, and its heating method is gas heati...
PUM
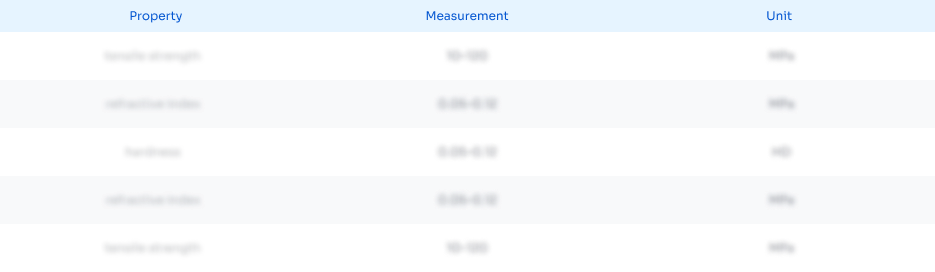
Abstract
Description
Claims
Application Information

- R&D Engineer
- R&D Manager
- IP Professional
- Industry Leading Data Capabilities
- Powerful AI technology
- Patent DNA Extraction
Browse by: Latest US Patents, China's latest patents, Technical Efficacy Thesaurus, Application Domain, Technology Topic, Popular Technical Reports.
© 2024 PatSnap. All rights reserved.Legal|Privacy policy|Modern Slavery Act Transparency Statement|Sitemap|About US| Contact US: help@patsnap.com