Inkjet infiltrating glazed porcelain tile and preparation method thereof
A technology of porcelain tiles and bleeding, which is applied in the field of architectural ceramics and can solve problems such as poor hardness, poor chemical corrosion resistance, and poor antifouling.
- Summary
- Abstract
- Description
- Claims
- Application Information
AI Technical Summary
Problems solved by technology
Method used
Image
Examples
Embodiment 1
[0046] A method for manufacturing inkjet bleed glazed porcelain tiles and products thereof
[0047] 1: Preparation of the bottom glaze of the seepage porcelain tile: In order to match the color development of the seepage ink, no calcium, magnesium, zinc, barium and other raw materials are added to the glaze slurry. The formula is as follows: 44 parts of potassium feldspar, 12 parts of albite, 6 parts of kaolin, 22 parts of burnt clay, 12 parts of quartz, 4 parts of zirconium silicate, additive A: 0.5 parts, additive B: 4 parts. The chemical composition analysis of additive A is SiO 2 2.01%, Al 2 o 3 2.89%, Fe 2 o 3 0.03%, TiO 2 93.05%, CaO0.03%, MgO0.09%, K 2 O0.02%, Na 2 O0.06%, balance is 1.35% impurity. The chemical composition analysis of Additive B is SiO 2 94.41%, Al 2 o 3 0.14%, Fe 2 o 3 0.05%, TiO 2 0.05%, CaO0.08%, MgO0.06%, K 2 O0.04%, Na 2 O0.21%, balance is 4.59% impurity. The chemical composition analysis of the bottom glaze is SiO 2 64.88%, Al ...
Embodiment 2
[0063] A method for manufacturing inkjet bleed glazed porcelain tiles and products thereof
[0064]1: Preparation of the bottom glaze of the seepage porcelain tile: In order to match the color development of the seepage ink, no calcium, magnesium, zinc, barium and other raw materials are added to the glaze slurry. The formula is as follows: 47 parts of potassium feldspar, 13 parts of albite, 6 parts of kaolin, 21 parts of burnt clay, 12 parts of quartz, 5 parts of zirconium silicate, additive A: 0.5 parts, additive B: 3 parts. The chemical composition analysis of additive A is SiO 2 2.01%, Al 2 o 3 2.89%, Fe 2 o 3 0.03%, TiO 2 93.05%, CaO0.03%, MgO0.09%, K 2 O0.02%, Na 2 O0.06%, balance is 1.35% impurity. The chemical composition analysis of Additive B is SiO 2 94.41%, Al 2 o 3 0.14%, Fe 2 o 3 0.05%, TiO 2 0.05%, CaO0.08%, MgO0.06%, K 2 O0.04%, Na 2 O0.21%, balance is 4.59% impurity. The chemical composition analysis of the bottom glaze is SiO 2 65.54%, Al 2...
PUM
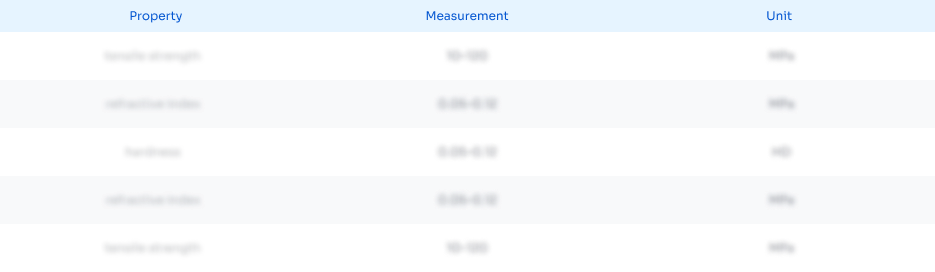
Abstract
Description
Claims
Application Information

- R&D
- Intellectual Property
- Life Sciences
- Materials
- Tech Scout
- Unparalleled Data Quality
- Higher Quality Content
- 60% Fewer Hallucinations
Browse by: Latest US Patents, China's latest patents, Technical Efficacy Thesaurus, Application Domain, Technology Topic, Popular Technical Reports.
© 2025 PatSnap. All rights reserved.Legal|Privacy policy|Modern Slavery Act Transparency Statement|Sitemap|About US| Contact US: help@patsnap.com