High power density hybrid excitation permanent magnet linear generator with ring yoke armature winding
A high power density, armature winding technology, applied in the shape/style/structure of winding conductors, magnetic circuit static parts, magnetic circuit shape/style/structure, etc., can solve the problem of increasing device possibilities, permanent magnet mechanical structure Damage, low material utilization, etc., to reduce the possibility of failure, eliminate mechanical stress damage, and high material utilization
- Summary
- Abstract
- Description
- Claims
- Application Information
AI Technical Summary
Problems solved by technology
Method used
Image
Examples
Embodiment 1
[0059] Example 1 as image 3 As shown, the number of stator teeth of the motor in this embodiment is 8, the number of teeth of the mover is 4, and the number of permanent magnet blocks is 4. This embodiment includes a stator, a mover, a main air gap and an additional air gap, and the stator includes a stator core, a permanent magnet and stator slots, the stator core includes stator teeth 1, stator back yoke 2 and stator slot yoke 3, the stator core is made of ferromagnetic material with high magnetic permeability, the stator core is provided with stator slots, and the stator slots include armature slots 5 and excitation slot 6, the armature slot 5 and the excitation slot 6 are alternately arranged at intervals, and the armature winding 6 is placed in the armature slot 4, and the armature winding 6 penetrates from one armature slot 4, and then moves outward along the back of the stator. The outer surface of the yoke 2 passes through to form a coil, the armature winding 6 surrou...
Embodiment 2
[0060] Example 2 as Figure 4 As shown, the number of stator teeth of the motor in this embodiment is 8, the number of teeth of the mover is 4, and the number of permanent magnet blocks is 8. This embodiment includes a stator, a mover, a main air gap and an additional air gap, and the stator includes a stator core and a permanent magnet. and stator slots, the stator core includes stator teeth 1, stator back yoke 2 and stator slot yoke 3, the stator core is made of ferromagnetic material with high magnetic permeability, the stator core is provided with stator slots, and the stator slots include armature slots 4 and excitation slot 5, armature slot 4 and excitation slot 6 are alternately arranged at intervals, armature winding 6 is placed in armature slot 4, armature winding 6 penetrates from one armature slot 4, and then moves outward along the back of the stator The outer surface of the yoke 2 passes through to form a coil, the armature winding 6 surrounds the stator slot yoke...
PUM
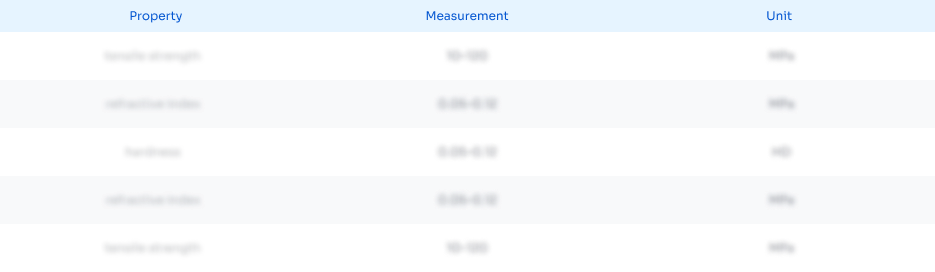
Abstract
Description
Claims
Application Information

- R&D Engineer
- R&D Manager
- IP Professional
- Industry Leading Data Capabilities
- Powerful AI technology
- Patent DNA Extraction
Browse by: Latest US Patents, China's latest patents, Technical Efficacy Thesaurus, Application Domain, Technology Topic, Popular Technical Reports.
© 2024 PatSnap. All rights reserved.Legal|Privacy policy|Modern Slavery Act Transparency Statement|Sitemap|About US| Contact US: help@patsnap.com