Assembled monolithic concrete frame structure system and frame shear structure system formed by assembled monolithic concrete frame structure system
A frame structure and concrete technology, used in building components, building structures, walls, etc., can solve the problems that the seismic resistance and overall performance of the structure cannot be fully guaranteed, cannot effectively prevent cross-inclined cracks, and affect the safe use of high-rise buildings. The effect of saving splicing time, convenient construction and simple connection structure
- Summary
- Abstract
- Description
- Claims
- Application Information
AI Technical Summary
Problems solved by technology
Method used
Image
Examples
Embodiment 1
[0052] Depend on Figure 1-Figure 7 An assembled monolithic concrete frame structure system shown includes prefabricated columns 1 , prefabricated beams 2 and prefabricated floor slabs 4 . Wherein the prefabricated column 1 is arranged vertically, and the prefabricated beam 2 and the prefabricated floor slab 4 are both arranged horizontally. Prefabricated columns 1 and prefabricated beams 2 form a frame body, several prefabricated columns 1 are arranged vertically and horizontally at intervals, and several prefabricated beams 2 are respectively arranged between two vertically adjacent precast columns 1 and between horizontally adjacent two prefabricated columns. The floor slab 4 is erected in the area enclosed by four prefabricated beams.
[0053] The prefabricated beam 2 is an ordinary reinforced concrete member, and the prefabricated beam 2 is provided with a prefabricated beam reinforcement cage 72, and a block-shaped prefabricated beam foam plastic inner mold 82 is embedded...
Embodiment 2
[0059] Depend on Figure 8-Figure 9 The difference between the assembled integral concrete frame structure system shown in Example 1 is that the prefabricated floor slab 4 adopts a prefabricated concrete hollow floor slab, and the prefabricated frame beams connected between the prefabricated columns 1 and the prefabricated beams 2 are connected by cover plates Column joint structural connection.
[0060] The ends of the prefabricated floor slabs 4 are erected on the top end faces of the corresponding prefabricated beams 2, and the prefabricated floor slabs 4 are formed by connecting several precast concrete hollow floor slabs 28 through end concrete transverse joints and slab side concrete longitudinal joints. The butt ends of the two precast concrete hollow slabs 28 are erected on the beam tops of the corresponding prefabricated beams 2, and a main grouting area 30 for concrete grouting is provided between the two butt ends of the two precast concrete hollow slabs 28, and the...
Embodiment 3
[0063] Depend on Figure 10-Figure 11 An assembled monolithic concrete frame structure system shown is different from Embodiment 1 or Embodiment 2 in that the prefabricated column 1 and the prefabricated beam 2 are connected through a fabricated frame beam-column node structure using transverse connections.
[0064] The assembled frame beam-column joint structure adopting horizontal connection includes the concealed corbel 41 set on the beam of the prefabricated column 1, the cross section of the concealed corbel 41 is rectangular, and the concealed corbel bolt holes are reserved horizontally on the concealed corbel 41; the prefabricated The front side of the joint of the end of the beam 2 is provided with a notch groove matched with the concealed corbel 41. The notch groove is to dig a gap from the vertical axis of the prefabricated beam 2 to one side, and the cross-sectional shape of the notch and the concealed corbel 41 Similarly, the size of the notch is slightly larger th...
PUM
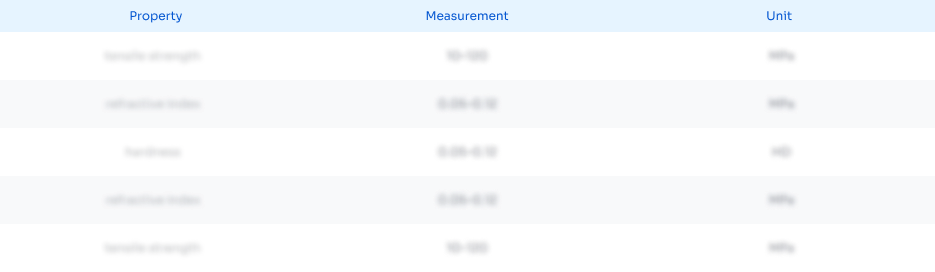
Abstract
Description
Claims
Application Information

- R&D
- Intellectual Property
- Life Sciences
- Materials
- Tech Scout
- Unparalleled Data Quality
- Higher Quality Content
- 60% Fewer Hallucinations
Browse by: Latest US Patents, China's latest patents, Technical Efficacy Thesaurus, Application Domain, Technology Topic, Popular Technical Reports.
© 2025 PatSnap. All rights reserved.Legal|Privacy policy|Modern Slavery Act Transparency Statement|Sitemap|About US| Contact US: help@patsnap.com