Flame-retardant microcapsule phase-change material
A technology of phase change materials and microcapsules, which is applied in the direction of microcapsule preparations, heat exchange materials, microsphere preparation, etc., can solve the problems of complex process, instability, poor water resistance and solvent resistance of phosphate ester, and achieve excellent performance, Improves smoothness and avoids negative effects
- Summary
- Abstract
- Description
- Claims
- Application Information
AI Technical Summary
Problems solved by technology
Method used
Examples
Embodiment 1
[0020] Under the condition of gentle stirring, the discontinuous phase 50g fatty acid ester, 25g PhosgardC-22-R, 25g pentaerythritol tetraacrylate (PETRA) and 2.5g BPO were stirred evenly and mixed thoroughly, and the continuous phase was mixed with 400g deionized water, 2.5g polyethylene Pyrrolidone (PVP) and 2.5g sodium dodecyl sulfate (SDS) were mixed uniformly in another reactor; the above-mentioned discontinuous phase was added to the continuous phase reactor, and stirred rapidly for 5 minutes, wherein the stirring speed was 3000rpm, and then Reduce the stirring speed to 300rpm, and raise the temperature to 75°C and keep it for 1.5 hours, then adjust the temperature to 90°C and keep it for 4 hours; stop heating and cool down to room temperature naturally; take out the suspension of microcapsule phase change material , and washed three times to remove unreacted monomers and uncoated monomers, and dried in an oven at 50°C for 48 hours to obtain a flame-retardant microcapsule...
Embodiment 2
[0022] Under the condition of gentle stirring, the discontinuous phase 50g fatty acid ester, 8g olefinic phosphonate, 8g pentaerythritol tetraacrylate (PETRA) and 0.3g BPO were stirred evenly and mixed thoroughly, and the continuous phase was mixed with 400g deionized water, 3.3g poly Vinyl alcohol (PVA) and 3.3g sodium dodecyl sulfate (SDS) were mixed evenly in another reactor; the above discontinuous phase was added to the continuous phase reactor, and stirred rapidly for 40 minutes, wherein the stirring speed was 3000rpm, and then Reduce the stirring speed to 300rpm, and raise the temperature to 75°C and keep it for 1.5 hours, then adjust the temperature to 90°C and keep it for 4 hours; stop heating and cool down to room temperature naturally; take out the microcapsule phase change material suspension, and washed 3 times to remove unreacted monomers and uncoated monomers, and dried in an oven at 50°C for 48 hours to obtain a flame-retardant microcapsule phase-change material...
Embodiment 3
[0024] In the case of gentle stirring, the discontinuous phase 50g fatty acid ester, 6.25g PyrpvatesCP, 6.25g pentaerythritol tetraacrylate (PETRA) and 0.36g BPO were stirred evenly and mixed thoroughly, and the continuous phase was 310g deionized water, 2.1gSpan-80 and 2.1 g sodium dodecylbenzene sulfonate (SDBS) was mixed evenly in another reactor; the above discontinuous phase was added to the continuous phase reactor, stirred rapidly for 20 minutes at a stirring speed of 3000rpm, and then the stirring speed was reduced to 300rpm , and raise the temperature to 75°C and keep it for 1.5 hours, then adjust the temperature to 90°C and keep it for 4 hours; stop the heating and cool down to room temperature naturally; take out the suspension of the microcapsule phase change material and wash it 3 times Remove unreacted monomers and uncoated monomers, and dry them in an oven at 50°C for 48 hours to obtain a flame-retardant microcapsule phase change material with a phase change enth...
PUM
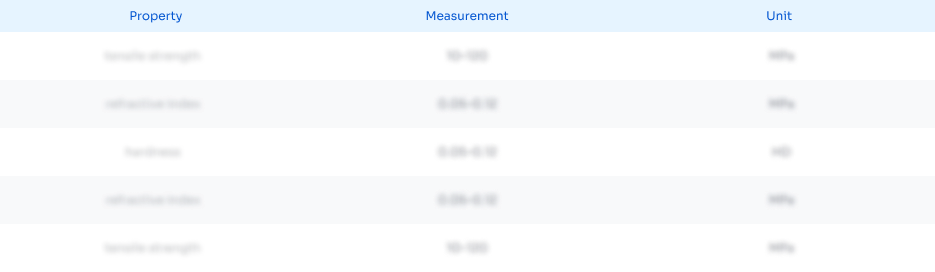
Abstract
Description
Claims
Application Information

- Generate Ideas
- Intellectual Property
- Life Sciences
- Materials
- Tech Scout
- Unparalleled Data Quality
- Higher Quality Content
- 60% Fewer Hallucinations
Browse by: Latest US Patents, China's latest patents, Technical Efficacy Thesaurus, Application Domain, Technology Topic, Popular Technical Reports.
© 2025 PatSnap. All rights reserved.Legal|Privacy policy|Modern Slavery Act Transparency Statement|Sitemap|About US| Contact US: help@patsnap.com