A gear local fault diagnosis method and system
A local fault and diagnosis method technology, which is applied in the direction of machine gear/transmission mechanism testing, etc., can solve problems such as easy failure, and achieve the effects of wide application range, avoiding low-frequency interference, and accurate diagnosis results
- Summary
- Abstract
- Description
- Claims
- Application Information
AI Technical Summary
Problems solved by technology
Method used
Image
Examples
Embodiment 1
[0038] Embodiment 1: as Figure 1-4 As shown, a gear local fault diagnosis method, including:
[0039] The signal acquisition step is to obtain the vibration signal of the faulty gear through the piezoelectric vibration acceleration sensor, and obtain the speed pulse signal of the shaft where the faulty gear is located through the eddy current displacement sensor;
[0040] The frequency domain filtering step is to perform band-pass filtering and noise reduction processing on the faulty gear vibration signal obtained in the signal acquisition step;
[0041] The spectral kurtosis calculation step is to calculate the optimal resonance frequency band {f o ,B o}, f o is the optimum resonant frequency, B o is the optimal bandwidth;
[0042] Angle-domain synchronous averaging step, the initial noise-reduced fault gear vibration signal obtained by the frequency-domain filtering step is converted into the angle domain and averaged to obtain the averaged angle-domain fault gear vib...
Embodiment 2
[0052] Embodiment 2: as Figure 1-4 Shown, basically the same as embodiment 1, on the basis of embodiment 1:
[0053] The frequency domain filtering step is specifically as follows: first transform the vibration signal of the faulty gear into the frequency domain through FFT, then set all the spectral lines outside the analysis frequency band (preferably 200-8000Hz) to zero, and then perform IFFT transformation to obtain a preliminary noise-reduced fault Gear vibration signal.
[0054] The spectral kurtosis calculation step is specifically: after the fault gear vibration signal of the preliminary noise reduction is obtained through the frequency domain filtering step, the fast spectral kurtosis diagram is used to calculate it to obtain the resonance frequency band {f c ,B c}, f c is the resonant frequency, B c is the bandwidth; use the maximum amplitude search method to search for the resonance frequency band {f c ,B c}, the frequency corresponding to the maximum amplitu...
Embodiment 3
[0061] Embodiment 3: as Figure 1-4 Shown, basically the same as embodiment 1, on the basis of embodiment 1:
[0062] The frequency domain filtering step is specifically as follows: first transform the vibration signal of the faulty gear into the frequency domain through FFT, then set all the spectral lines outside the analysis frequency band (preferably 200-8000Hz) to zero, and then perform IFFT transformation to obtain a preliminary noise-reduced fault Gear vibration signal.
[0063] The spectral kurtosis calculation step is specifically: after the fault gear vibration signal of the preliminary noise reduction is obtained through the frequency domain filtering step, the fast spectral kurtosis diagram is used to calculate it to obtain the resonance frequency band {f c ,B c}, f c is the resonant frequency, B c is the bandwidth; use the maximum amplitude search method to search for the resonance frequency band {f c ,B c}, the frequency corresponding to the maximum amplitu...
PUM
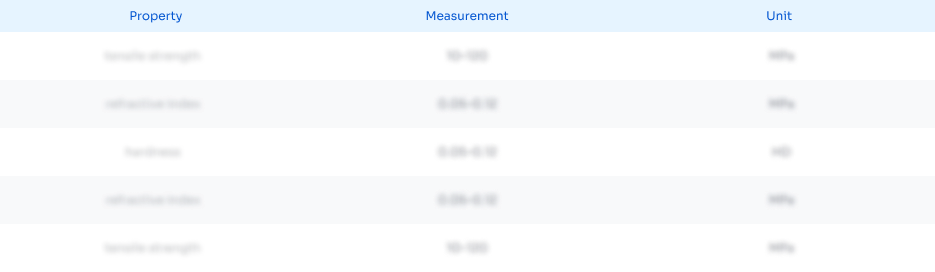
Abstract
Description
Claims
Application Information

- Generate Ideas
- Intellectual Property
- Life Sciences
- Materials
- Tech Scout
- Unparalleled Data Quality
- Higher Quality Content
- 60% Fewer Hallucinations
Browse by: Latest US Patents, China's latest patents, Technical Efficacy Thesaurus, Application Domain, Technology Topic, Popular Technical Reports.
© 2025 PatSnap. All rights reserved.Legal|Privacy policy|Modern Slavery Act Transparency Statement|Sitemap|About US| Contact US: help@patsnap.com