High-sensitivity distribution type hydrostatic pressure sensor and method of measuring fluid environment pressure by using high-sensitivity distribution type hydrostatic pressure sensor
A high-sensitivity, distributed technology, applied in the optical field, can solve the problems of low accuracy of hydrostatic pressure sensors, and achieve the effects of high spatial resolution, high sensitivity, and high sensing sensitivity
- Summary
- Abstract
- Description
- Claims
- Application Information
AI Technical Summary
Problems solved by technology
Method used
Image
Examples
specific Embodiment approach 1
[0043] Specific implementation mode one: the following combination figure 1 Describe this embodiment, the high-sensitivity distributed hydrostatic pressure sensor described in this embodiment includes a first tunable laser module 1, a second tunable laser module 2, a sensing fiber 3, a polarization beam splitter 4, Photodetector 5, fiber optic circulator 6, data acquisition card 7 and third tunable laser module 10;
[0044] The output frequency of the first tunable laser module 1 is ν 0 A continuous laser beam, the laser beam is a single polarization continuous laser beam whose polarization state is consistent with the x-axis of the sensing fiber 3, and the laser beam is injected into the +x axis of the sensing fiber 3;
[0045] The output frequency of the second tunable laser module 2 is ν 1 CW laser, the laser beam is a single polarization CW laser whose polarization state is consistent with the x-axis of the sensing fiber 3, and the frequency ν 0 with ν 1 There is a fib...
specific Embodiment approach 2
[0053] Specific implementation mode two: the following combination figure 2 Describe this embodiment. Compared with Embodiment 1, this embodiment adds a signal generator 8 and an electro-optic modulator 9, and the frequency emitted by the third tunable laser 10 is ν 2 continuous laser light rather than pulsed light.
[0054] See the specific structure figure 2 , the high-sensitivity distributed hydrostatic pressure sensor, which includes a first tunable laser module 1, a second tunable laser module 2, a sensing fiber 3, a polarization beam splitter 4, a photodetector 5, an optical fiber ring 6, data acquisition card 7, signal generator 8, electro-optic modulator 9 and the third tunable laser module 10;
[0055] The output frequency of the first tunable laser module 1 is ν 0 A continuous laser beam, the laser beam is a single polarization continuous laser beam whose polarization state is consistent with the x-axis of the sensing fiber 3, and the laser beam is injected into...
specific Embodiment approach 3
[0061] Specific implementation mode three: This implementation mode further explains the first or second implementation mode, the first tunable laser module 1 and the second tunable laser module 2 are replaced by a laser, and the laser uses microwave modulation to form two beams Frequency ν 0 with ν 1 The laser, the frequency difference between the two laser beams is a fiber Brillouin frequency shift Δν B .
PUM
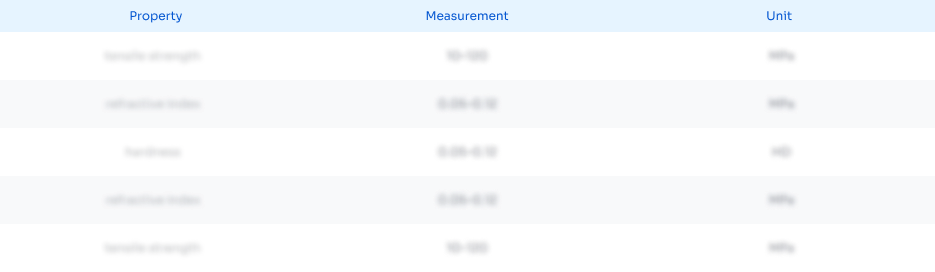
Abstract
Description
Claims
Application Information

- Generate Ideas
- Intellectual Property
- Life Sciences
- Materials
- Tech Scout
- Unparalleled Data Quality
- Higher Quality Content
- 60% Fewer Hallucinations
Browse by: Latest US Patents, China's latest patents, Technical Efficacy Thesaurus, Application Domain, Technology Topic, Popular Technical Reports.
© 2025 PatSnap. All rights reserved.Legal|Privacy policy|Modern Slavery Act Transparency Statement|Sitemap|About US| Contact US: help@patsnap.com