Method for making blister copper from highly magnetic copper oxide slag in one step and kiln for making blister copper
A copper oxide slag, high magnetic technology, applied in the direction of improving process efficiency, can solve the problems of low reduction efficiency of electric furnace, easy formation of frozen layer at the bottom of the furnace, low recovery rate of beneficiation, etc., to reduce the amount of high magnetic copper oxide slag, The effect of facilitating sedimentation and separation and improving the direct yield
- Summary
- Abstract
- Description
- Claims
- Application Information
AI Technical Summary
Problems solved by technology
Method used
Image
Examples
Embodiment 1
[0016] figure 1 Shown is a schematic diagram of a kiln for carrying out the method of the present invention. The furnace body 1 of the kiln is a cylindrical furnace body that is horizontally installed on the seat ring 2 and can rotate axially. The top of the furnace body is provided with a feed port 3, and the bottom of the furnace body is provided with a tuyere 4 arranged in a straight line. There is a cyclone piece, and the tuyere can be used to switch the injection of compressed oxygen-enriched air and nitrogen. The upper front end of the furnace body is provided with a slag receiving port 5, the rear end of the furnace body is provided with a burner 6, and the upper part of the furnace wall is provided with a blister copper discharge port 7 for discharging blister copper after slag removal. The rotation angle of the cylindrical furnace body 1 is 90°-270°. In actual production, the slag outlet 5 of the furnace body can be connected to the slag outlet 10 of the blowing fur...
Embodiment 2
[0025] Such as figure 1 As shown, the highly magnetic copper oxide slag is discharged from the slag outlet 10 of the top-blown furnace 9 through the chute 8 to the slag outlet 5 of the kiln and enters the furnace body 1. The slag outlet is also the flue gas discharge during the smelting process of the furnace The flue gas is discharged to the environmental protection flue gas treatment system through the discharge port and then sent to the chimney for discharge. Furnace burner 6 can burn diesel oil, heavy oil or natural gas, etc., and use oxygen-enriched combustion to maintain the temperature of the furnace chamber at 1300°C-1320°C, and the high-magnetic copper oxide slag melt at 1250°C-1270°C. High Magnetic Copper Oxide Slag Fe / SiO 2 The ratio is controlled at 1.5 to 1.8 to keep a certain amount of free quartz in the oxidation slag. The copper concentrate bin 12 is pre-installed with 150 tons of copper concentrate with a grade of 20-25% for reducing the oxidation slag. Aft...
PUM
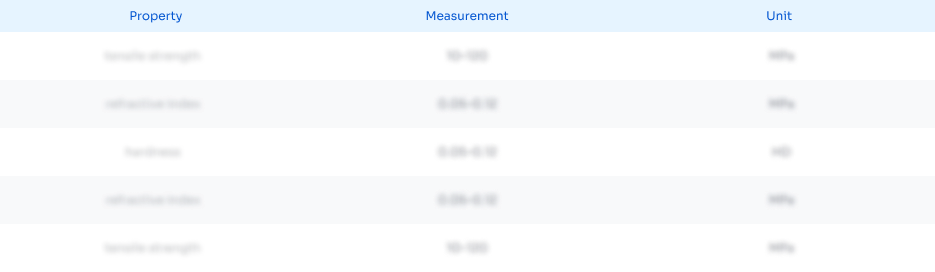
Abstract
Description
Claims
Application Information

- Generate Ideas
- Intellectual Property
- Life Sciences
- Materials
- Tech Scout
- Unparalleled Data Quality
- Higher Quality Content
- 60% Fewer Hallucinations
Browse by: Latest US Patents, China's latest patents, Technical Efficacy Thesaurus, Application Domain, Technology Topic, Popular Technical Reports.
© 2025 PatSnap. All rights reserved.Legal|Privacy policy|Modern Slavery Act Transparency Statement|Sitemap|About US| Contact US: help@patsnap.com