Water-jet machining device
A processing device and water jet technology, which is applied in metal processing equipment, used abrasive processing devices, manufacturing tools, etc., can solve the problem of high wear rate of nozzles and sand mixing chambers, wear of sand mixing chambers and nozzles, and affecting processing capacity. and other problems to achieve consistent control, reduce maintenance costs, and control wear and tear.
- Summary
- Abstract
- Description
- Claims
- Application Information
AI Technical Summary
Problems solved by technology
Method used
Image
Examples
Embodiment 1
[0050] like figure 2 As shown, the inner wall of the outlet 223 of the shaping tube is a smooth inner wall, and the length of the nozzle 230 is relatively short. In the sand mixing chamber 210, the mixed liquid after mixing the abrasive and high-pressure water is sprayed out through the outlet of the sand mixing chamber 210 to form a central water jet. The flow velocity of the mixed liquid in the sand mixing chamber 210 is relatively low, and the flow velocity of the mixed liquid in the sand mixing chamber 210 is much lower than that of the central water jet. The flow velocity of the mixed liquid in the traditional high-pressure sand mixing chamber is greater than 400 m / s, but in this embodiment, the flow velocity of the mixed liquid in the sand mixing chamber 210 is lower than 20 m / s. In this way, the wear of the abrasive on the inner wall of the sand mixing chamber 210 is much smaller than that of a traditional high-pressure sand mixing chamber, reducing the wear rate of t...
Embodiment 2
[0054] like image 3 As shown, in order to further enhance the wrapping degree of the buffer medium on the central water jet, the inner wall of the outlet 223 of the shaping tube can be designed as a non-smooth inner wall with a geometric structure. Preferably, the inner wall of the outlet 223 of the shaping tube is provided with a helical slot 224, so that the buffer medium produces a helical effect before merging with the central water jet, so as to improve the stability of the package. According to the simulation results of the experiment, it can be seen that the shaping tube 220 with the helical slot 224 can better maintain the stability of the central water jet and improve the kinetic energy of the central water jet than the smooth shaping tube 220 .
Embodiment 3
[0056] like Figure 4 As shown, in this embodiment, the nozzle 230 is a linear narrow structure, and by controlling the outer diameter of the nozzle 230, the nozzle 230 can go deep into a narrow space for processing. Preferably, the outer diameter of the nozzle 230 is less than 3 mm, the inner diameter is less than 50 microns, and the length of the nozzle 230 is greater than 100 mm. In the conventional technology, since the abrasive directly contacts the inner wall of the nozzle 230 , the wear of the abrasive on the nozzle 230 will greatly reduce the service life of the nozzle 230 , so the length of the nozzle 230 is relatively short. In this embodiment, the length of the nozzle 230 can be designed longer and the diameter of the nozzle 230 can be designed smaller because the buffer medium reduces the wear rate of the nozzle 230 . In this embodiment, the material of the nozzle 230 is tungsten carbide, and the hole shape of the nozzle 230 is circular. Certainly, the material o...
PUM
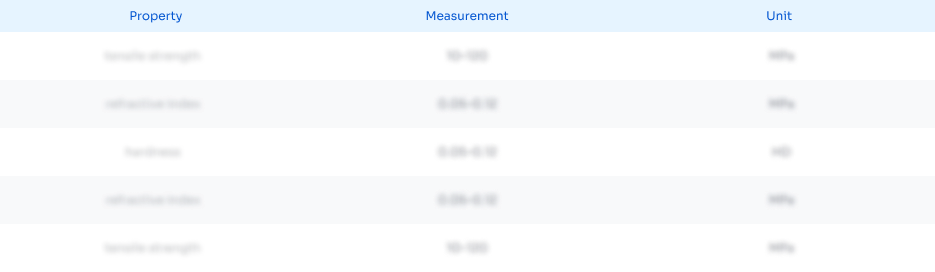
Abstract
Description
Claims
Application Information

- Generate Ideas
- Intellectual Property
- Life Sciences
- Materials
- Tech Scout
- Unparalleled Data Quality
- Higher Quality Content
- 60% Fewer Hallucinations
Browse by: Latest US Patents, China's latest patents, Technical Efficacy Thesaurus, Application Domain, Technology Topic, Popular Technical Reports.
© 2025 PatSnap. All rights reserved.Legal|Privacy policy|Modern Slavery Act Transparency Statement|Sitemap|About US| Contact US: help@patsnap.com