a recycling no x Desulfurization and denitrification co-production calcium sulfate whisker process
A technology of calcium sulfate whisker, desulfurization and denitrification, applied in the direction of calcium/strontium/barium sulfate, nitric acid, nitrogen oxides/oxyacids, etc., can solve the problems of low by-product value, high consumption value and large investment, etc. Achieve the effect of less sulfate radicals and less direct current consumption
- Summary
- Abstract
- Description
- Claims
- Application Information
AI Technical Summary
Problems solved by technology
Method used
Image
Examples
Embodiment 1
[0048] figure 1 Medium desulfurization and denitrification absorption tower 1, electrolysis device 2, filter 3, filtrate tank 4, washing liquid tank 5, slurry tank 6, slurry pump 7, filtrate pump 8, washing liquid pump 9, slurry pump 10, vacuum pump 11; Lime powder A, flue gas B, recovered NOx gas C, purified flue gas D, washing process water E, gypsum whiskers F.
[0049] The flue gas B at a temperature of 150°C enters the middle part of the desulfurization and denitrification absorption tower 1, and is in countercurrent contact with the circulating slurry, feed slurry, filtrate and washing process water sprayed from the upper part. The circulation of the slurry in the tower can be set or not, as shown in Fig. Not shown in the figure, the slurry in the tower flows through the electrolysis device 2 outside the tower, one part flows into the feeding slurry tank 6 to make slurry with the input lime powder A, and then is sent to the desulfurization and denitrification absorption ...
Embodiment 2
[0053] figure 2 Medium desulfurization and denitrification absorption tower 1, slurry tank 2, filter 3, filtrate tank 4, washing liquid tank 5, slurry pump 6, slurry pump 7, filtrate pump 8, washing liquid pump 9, vacuum pump 10; lime powder A, Flue gas B, purified flue gas C, recovered NOx gas D, washing process water E, gypsum whiskers F.
[0054] The flue gas B at a temperature of 150°C enters the middle part of the desulfurization and denitrification absorption tower 1, and is in countercurrent contact with the circulating slurry, feed slurry, filtrate and washing process water sprayed from the upper part. The circulation of the slurry in the tower can be set or not, as shown in Fig. Not shown in the figure, the slurry in the tower is output by the slurry pump 6, one part is sent to the slurry tank 2 to make slurry with the input lime powder A, and then sent to the desulfurization and denitrification absorption tower 1 by the slurry pump 7, and one part is sent to the fil...
Embodiment 3
[0058] image 3 Medium desulfurization and denitrification absorption tower 1, filter 2, slurry tank 3, washing liquid tank 4, slurry pump 5, circulating slurry pump 6, vacuum pump 7, slurry pump 8, washing liquid pump 9; flue gas A, purify flue gas B, recovery of NOx gas C, washing process water D, lime powder E, gypsum whiskers F.
[0059] The flue gas A at a temperature of 150°C enters the middle part of the desulfurization and denitrification absorption tower 1, and is in countercurrent contact with the circulating slurry, feed slurry and washing process water sprayed from the upper part. Most of the slurry in the tower is circulated by the circulating slurry pump 6, and a small part The output of the slurry pump 5 is sent to the filter 2 for filtration, the filtrate and the input lime powder E are slurried in the slurry tank 3 and then sent to the desulfurization and denitrification absorption tower 1 by the slurry pump 8, and the filtered solid phase is washed with the w...
PUM
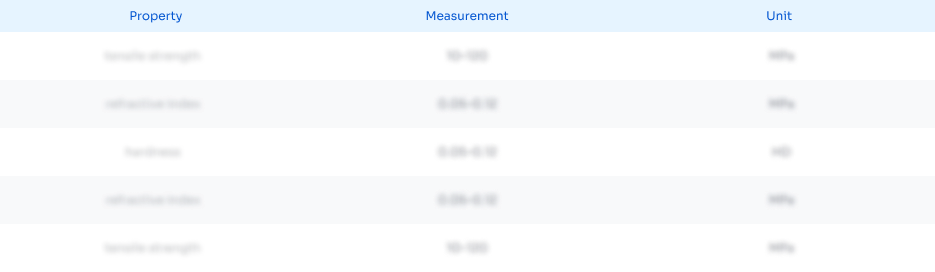
Abstract
Description
Claims
Application Information

- R&D Engineer
- R&D Manager
- IP Professional
- Industry Leading Data Capabilities
- Powerful AI technology
- Patent DNA Extraction
Browse by: Latest US Patents, China's latest patents, Technical Efficacy Thesaurus, Application Domain, Technology Topic, Popular Technical Reports.
© 2024 PatSnap. All rights reserved.Legal|Privacy policy|Modern Slavery Act Transparency Statement|Sitemap|About US| Contact US: help@patsnap.com