Full-web type steel box transfer beam and connecting structure of full-web type steel box transfer beam and reinforced concrete shear wall
A technology for converting beams and concrete, applied in building structures, walls, building components, etc., can solve the problems of high connection cost, increased foundation load, and increased construction cost, and achieves improved pouring efficiency, reduced structural cost, and reduced foundation load. Effect
- Summary
- Abstract
- Description
- Claims
- Application Information
AI Technical Summary
Problems solved by technology
Method used
Image
Examples
Embodiment 1
[0044] Such as Figure 2 to Figure 7 As shown, the solid-web steel box transfer girder according to Embodiment 1 of the present invention includes a steel box girder and concrete 9 . in, figure 2 shows the four solid-web steel box transfer beams Z1~Z4 applied in a transfer layer, the two adjacent supports J1 and J2 of the solid-web steel box transfer beam Z1, and the solid-web steel box transfer The two adjacent supports J3 and J4 of the beam Z2, among them, the support J1 is the beam-column joint between the solid-web steel box transfer beam Z1 and the structural column G1, and the support J2 is the solid-web steel box transfer beam Z1 and the structural Beam-column connection for column G2.
[0045] The above-mentioned steel box girder has a tubular main body connected by a top plate 1, a bottom plate 2, and two webs 3. The inner cavity a of the tubular main body is provided with a plurality of transverse partitions 4 distributed along the axial direction of the tubular m...
Embodiment 2
[0052] Such as Figure 8-1 to Figure 8-3 As shown, the solid-web steel box transfer girder of the second embodiment of the present invention is basically the same as the first embodiment, and their difference is that in the second embodiment, the inner cavity a of the tubular main body of the steel box girder is provided with a longitudinal partition 10, the longitudinal partition 10 extends along the axial direction of the tubular body and divides the inner cavity a of the tubular body into an upper chamber a1 and a lower chamber a2; the concrete flow hole 4a is located in the upper chamber a1, and the concrete 9 is filled In the upper chamber a1, there is no concrete filling in the lower chamber a2; the four concrete flow gaps 4b of the transverse partition 4 are respectively arranged at the four corners of the part of the transverse partition 4 located in the upper chamber a1. Through such setting, when the solid-web steel box transfer beam of the second embodiment is subje...
Embodiment 3
[0054] Such as Figure 9 to Figure 11As shown, the connection structure between the transfer beam and the reinforced concrete shear wall according to the third embodiment of the present invention includes the transfer beam and the reinforced concrete shear wall 11 arranged on the transfer beam. Wherein, the transfer beam in the third embodiment adopts the solid-web steel box transfer beam, and the solid-web steel box transfer beam in the third embodiment is basically the same as the above-mentioned embodiment 1 or embodiment 2, except that: The solid-web steel box transfer beam in the third embodiment is provided with two steel plates 13 for connecting the reinforced concrete shear wall 11 on the upper end surface of the top plate 1 outside the concrete pouring opening 1a, and the two steel plates 13 are both Extends axially along the tubular body. Among the two rows of steel bars of the reinforced concrete shear wall 11 in the third embodiment, the lower ends of the steel ba...
PUM
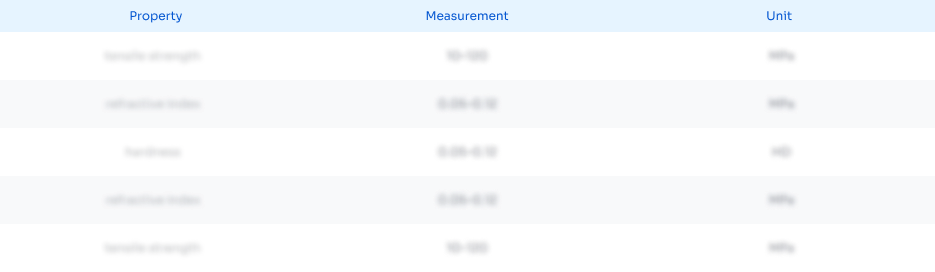
Abstract
Description
Claims
Application Information

- Generate Ideas
- Intellectual Property
- Life Sciences
- Materials
- Tech Scout
- Unparalleled Data Quality
- Higher Quality Content
- 60% Fewer Hallucinations
Browse by: Latest US Patents, China's latest patents, Technical Efficacy Thesaurus, Application Domain, Technology Topic, Popular Technical Reports.
© 2025 PatSnap. All rights reserved.Legal|Privacy policy|Modern Slavery Act Transparency Statement|Sitemap|About US| Contact US: help@patsnap.com