Current Compensation Method for Bearingless Rotor Vibration Unbalance Based on Random Displacement Inverse
A technology of random displacement and balanced current, applied in the direction of controlling electromechanical brakes, controlling electromechanical transmission devices, electrical components, etc., can solve problems such as assembly errors, unbalanced vibration suppression effects, uneven materials, etc.
- Summary
- Abstract
- Description
- Claims
- Application Information
AI Technical Summary
Problems solved by technology
Method used
Image
Examples
Embodiment Construction
[0044] In order to make the content of the present invention more obvious and understandable, the present invention will be described in detail below in conjunction with specific examples.
[0045] Core idea of the present invention is:
[0046] 1. During the rotation of the bearingless motor rotor, the inevitable rotor mass eccentricity will excite the excitation force in the same direction as the eccentricity; if no vibration control measures are added, under the action of the excitation force, the rotor shaft will The heart produces periodic radial displacement fluctuations or vibrations, that is, unbalanced displacement. The unbalanced displacement signal of the rotor of a bearingless asynchronous motor is a sinusoidal alternating signal with the same frequency as the rotational speed. Based on this feature, real-time filtering, tracking and extraction of the unbalanced displacement signal can be carried out, and the radial displacement of the rotor can be separated into...
PUM
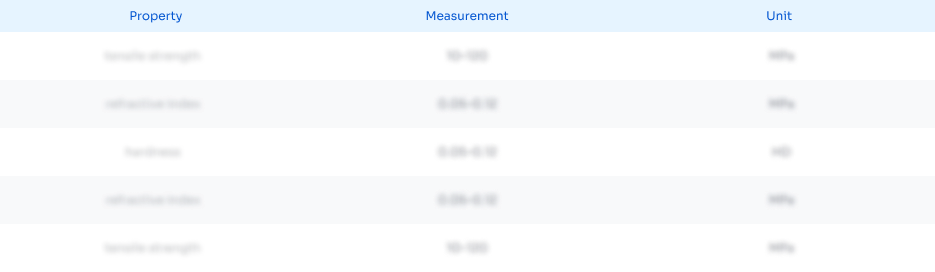
Abstract
Description
Claims
Application Information

- R&D Engineer
- R&D Manager
- IP Professional
- Industry Leading Data Capabilities
- Powerful AI technology
- Patent DNA Extraction
Browse by: Latest US Patents, China's latest patents, Technical Efficacy Thesaurus, Application Domain, Technology Topic, Popular Technical Reports.
© 2024 PatSnap. All rights reserved.Legal|Privacy policy|Modern Slavery Act Transparency Statement|Sitemap|About US| Contact US: help@patsnap.com