Test device for dynamically measuring fretting pair frictional coefficient during fretting fatigue process and test method
A friction coefficient and fretting fatigue technology, applied in measuring devices, mechanical devices, instruments, etc., can solve the problems of inability to provide fretting fatigue conditions, small driving force of thread loading scheme, and variation of loading normal force, etc. Accurate prediction of fretting fatigue life, reliable test results, and the effect of preventing local stress concentration
- Summary
- Abstract
- Description
- Claims
- Application Information
AI Technical Summary
Problems solved by technology
Method used
Image
Examples
Embodiment Construction
[0046] Please refer to Figure 1 to Figure 8 As shown, the test device for dynamically measuring the friction coefficient of the fretting pair in the process of fretting fatigue according to the present invention includes a friction coefficient measuring component 1 , a normal force loading component 2 and an upper end fixing component 3 .
[0047] The friction coefficient measurement assembly 1 includes a clamp body 11, a first compression cover plate 12 and a second compression cover plate 13 installed on the clamp body 11, an M6 compression bolt 14, a micro-movement pad clamping slider 15 and a micro-movement Pad 16. Wherein the clamping body 11 includes a first suspension part 110 and a second suspension part 117 located at its upper end and spaced apart left and right, extending downward from the lower end of the first suspension part 110 and the lower end of the second suspension part 117 respectively The formed first working part 111 and the second working part 118, th...
PUM
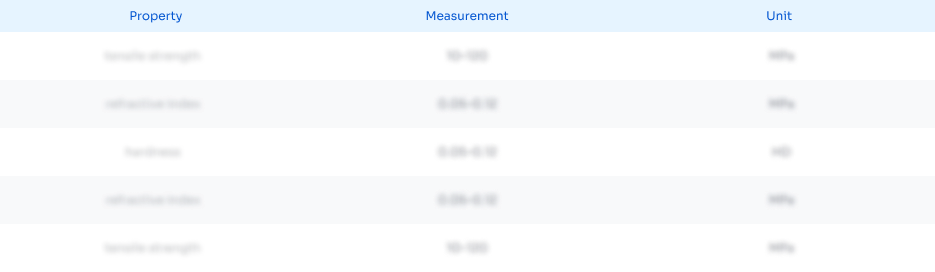
Abstract
Description
Claims
Application Information

- Generate Ideas
- Intellectual Property
- Life Sciences
- Materials
- Tech Scout
- Unparalleled Data Quality
- Higher Quality Content
- 60% Fewer Hallucinations
Browse by: Latest US Patents, China's latest patents, Technical Efficacy Thesaurus, Application Domain, Technology Topic, Popular Technical Reports.
© 2025 PatSnap. All rights reserved.Legal|Privacy policy|Modern Slavery Act Transparency Statement|Sitemap|About US| Contact US: help@patsnap.com