Double-side etching high-temperature and high-pressure printed circuit board heat exchanger
A printed circuit board, high temperature and high pressure technology, applied in the direction of heat exchanger type, indirect heat exchanger, laminated components, etc. Uneven distribution, affecting the safety of heat exchanger operation, etc., to achieve the effect of improving flow uniformity distribution, increasing heat exchange area utilization, and reducing thermal stress
- Summary
- Abstract
- Description
- Claims
- Application Information
AI Technical Summary
Problems solved by technology
Method used
Image
Examples
Embodiment Construction
[0031] The present invention will be described in detail below in conjunction with the accompanying drawings and specific embodiments.
[0032] refer to figure 1 As shown, a double-sided etching high-temperature and high-pressure heat exchanger includes: a core 1, which is divided into three parts according to the arrangement of the etching flow channel, the front section 2 of the core body is the inlet diversion section, the middle section 3 of the core body, and the back section of the core body Section 4 is the outlet diversion section, the hot-side inlet pipe 6 and the cold-side outlet pipe 8 are connected to the front section 2 of the core body through the expansion section 5, and the hot-side outlet pipe 7 and the cold-side inlet pipe 9 are connected to the core through the flow expansion section 5 The rear section 4 of the body ensures countercurrent heat exchange in the core heat exchange area of the middle section 3 of the core body.
[0033] refer to figure 2 As...
PUM
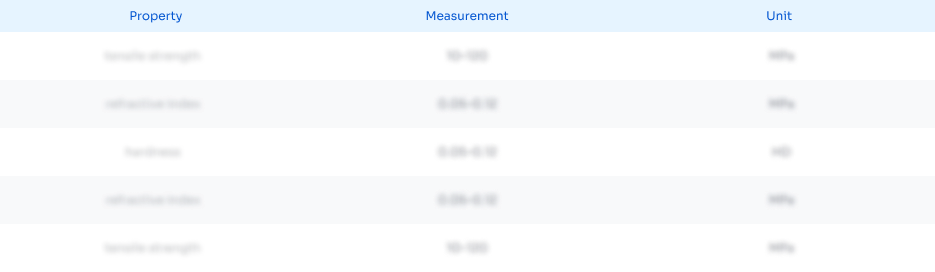
Abstract
Description
Claims
Application Information

- R&D Engineer
- R&D Manager
- IP Professional
- Industry Leading Data Capabilities
- Powerful AI technology
- Patent DNA Extraction
Browse by: Latest US Patents, China's latest patents, Technical Efficacy Thesaurus, Application Domain, Technology Topic, Popular Technical Reports.
© 2024 PatSnap. All rights reserved.Legal|Privacy policy|Modern Slavery Act Transparency Statement|Sitemap|About US| Contact US: help@patsnap.com