Modified scrap rubber powder as well as preparation method and application thereof
A waste rubber powder and modification technology, which is applied in recycling technology, plastic recycling, etc., can solve the problems of pollution promotion and use, limited modification effect, complicated process, etc., and achieve simplified process and equipment, reduced material cost, and excellent performance Effect
- Summary
- Abstract
- Description
- Claims
- Application Information
AI Technical Summary
Problems solved by technology
Method used
Image
Examples
Embodiment 1
[0037] A preparation method of modified waste rubber powder, specifically comprising the following steps:
[0038] (1) masticating 100 parts by mass of waste rubber powder and 1 part by mass of peptizer 2,2'-dibenzamidodiphenyl disulfide at 180°C for 2 minutes to obtain activated rubber powder;
[0039] (2) Mix 10 parts by mass of coupling agent KH900 with 100 parts by mass of epoxidized natural rubber (epoxy degree is 20) at 100° C. for 5 minutes to obtain a modifier;
[0040] (3) Add 10 parts by mass of modifier to 100 parts by mass of activated rubber powder, mix at 120° C. for 5 minutes, and obtain modified waste rubber powder after cooling. The structural characterization of the modified waste rubber powder is as follows: figure 2 shown. The structural characterization of unmodified waste rubber powder is as follows: figure 1 shown.
[0041] From figure 1 , figure 2 It can be seen that after the waste rubber powder is modified, the surface of the rubber powder is ...
Embodiment 2
[0042] Example 2 (modified rubber powder vulcanizate and unmodified rubber powder vulcanizate)
[0043] A preparation method of modified waste rubber powder, specifically comprising the following steps:
[0044] (1) masticating 100 parts by mass of waste rubber powder and 0.1 part by mass of peptizer pentachlorothiophenol at room temperature for 20 minutes to obtain activated rubber powder;
[0045] (2) Mix 8 parts by mass of coupling agent KH550 with 100 parts by mass of epoxidized natural rubber (40 degrees of epoxy) at 80° C. for 10 minutes to obtain a modifier;
[0046] (3) Add 12 parts by mass of modifier to 100 parts by mass of activated rubber powder, and mix at room temperature for 15 minutes to obtain modified waste rubber powder.
[0047] Preparation of rubber powder vulcanizate:
[0048]Add the same compounding agent (zinc oxide 4 weight parts, stearic acid 2 weight parts, accelerator CZ1. parts by weight, 0.5 parts by weight of accelerator DM, 2 parts by weight ...
Embodiment 3
[0052] Embodiment 3 (NR / modified waste rubber powder composite material)
[0053] A kind of application of modified waste rubber powder is the preparation of rubber / rubber powder composite material:
[0054] According to the commonly used rubber formulation, 100 parts by weight of natural rubber is added with compounding agents (4 parts by weight of zinc oxide, 2 parts by weight of stearic acid, 1.5 parts by weight of accelerator CZ, 0.5 parts by weight of accelerator DM, 2 parts by weight of sulfur parts), then respectively add 20 parts by weight of unmodified waste rubber powder and 10 to 30 parts by weight of the modified waste rubber powder prepared in Example 2, mix at 130°C for 5min, and then press the curing time T90 at 150°C Vulcanization and pressing to obtain NR / modified waste rubber powder composite materials and NR / unmodified waste rubber powder composite materials. The performance test results of the obtained vulcanized rubber materials, namely NR / modified waste ...
PUM
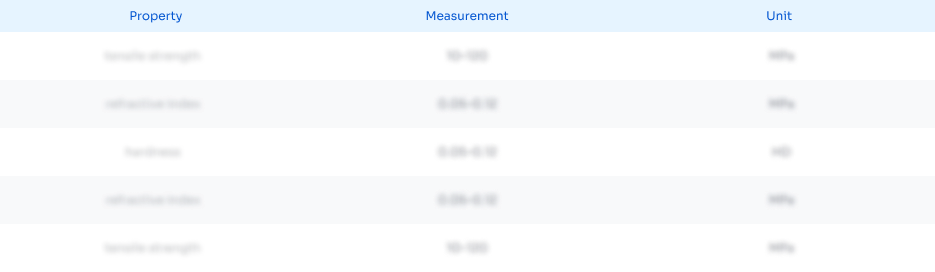
Abstract
Description
Claims
Application Information

- R&D
- Intellectual Property
- Life Sciences
- Materials
- Tech Scout
- Unparalleled Data Quality
- Higher Quality Content
- 60% Fewer Hallucinations
Browse by: Latest US Patents, China's latest patents, Technical Efficacy Thesaurus, Application Domain, Technology Topic, Popular Technical Reports.
© 2025 PatSnap. All rights reserved.Legal|Privacy policy|Modern Slavery Act Transparency Statement|Sitemap|About US| Contact US: help@patsnap.com