Wear-resistant finned tubes and heat exchangers
An anti-wear, finned tube technology, applied in tubular elements, heat exchange equipment, lighting and heating equipment, etc., can solve the problem of rigidity, low elastic compensation capacity, high heat transfer efficiency of finned tubes, poor heat transfer enhancement effect, etc. problems, to achieve the effect of improving flow field conditions, large heat transfer area, and reducing wear rate
- Summary
- Abstract
- Description
- Claims
- Application Information
AI Technical Summary
Problems solved by technology
Method used
Image
Examples
Embodiment 1
[0043] As shown in Figure 1 and Figure 2. The fin tube of the present invention comprises a base tube 1 and fins 3, wherein 1 is a base tube, and the fin 3 is a spiral fin. A rectangular drainage groove 2 is provided on the facing surface of the spiral fin, which is similar to a C shape. In this embodiment, the height of the drainage groove is 2 / 3 of the height of the fin, and the width of the drainage groove is 1 of the diameter of the base pipe. / 5, welding the slotted spiral fins to the base tube 1, or slotting the fins 3 of the existing spiral fin tubes.
[0044] Apply Fluent commercial software to the traditional spiral finned tube of a certain structural size ( Figure 5 , Figure 6 ), H-type finned tube (Figure 7, Figure 8) and the slotted spiral finned tube of the present invention (Figure 1, Figure 2) for numerical simulation of the external flue gas flow:
[0045] The flue gas velocity outside the finned tube is 6m / s, and flows along the positive direction of the x...
Embodiment 2
[0054] Shown in Figure 3 and Figure 4. The C-shaped circular finned tube of the present invention includes a base tube 1 and fins 3, wherein 1 is a base tube, and the fins 3 are circular parallel fins. A rectangular drainage groove 2 is provided on the facing surface of the spiral fin. In this embodiment, the height of the drainage groove is 4 / 5 of the height of the fin, and the width of the drainage groove is 1 / 5 of the diameter of the base pipe. The simulation obtains the C-type circular fin tube of the present invention and the traditional circular fin tube ( Figure 9 , Figure 10 ) The wear rate diagram of the upstream surface of the base pipe is shown in Figure 15 .
[0055] Depend on Figure 15 It can be seen that the wear rate of the base tube of the C-type circular finned tube of the present invention is lower than that of the traditional circular finned tube, and the wear area is also smaller than that of the traditional circular finned tube. The wear rate of t...
PUM
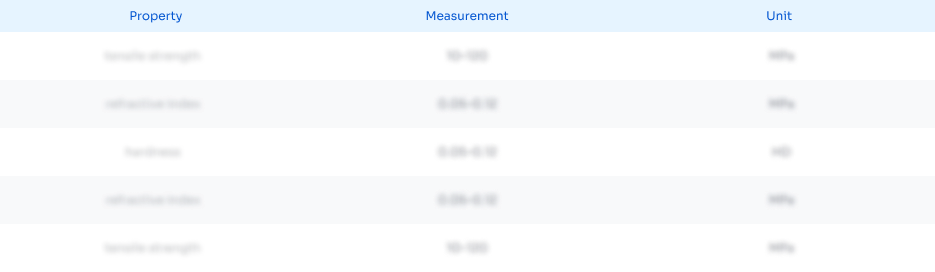
Abstract
Description
Claims
Application Information

- Generate Ideas
- Intellectual Property
- Life Sciences
- Materials
- Tech Scout
- Unparalleled Data Quality
- Higher Quality Content
- 60% Fewer Hallucinations
Browse by: Latest US Patents, China's latest patents, Technical Efficacy Thesaurus, Application Domain, Technology Topic, Popular Technical Reports.
© 2025 PatSnap. All rights reserved.Legal|Privacy policy|Modern Slavery Act Transparency Statement|Sitemap|About US| Contact US: help@patsnap.com