Method for synchronously separating iron, vanadium and manganese in vanadium extracting tailings
A technology for extracting vanadium tailings and synchronizing separation is applied in the field of metallurgy, which can solve problems such as separation of metals such as iron and vanadium not involved, and achieve the effects of improving resource utilization rate, high metal recovery rate and less waste.
- Summary
- Abstract
- Description
- Claims
- Application Information
AI Technical Summary
Problems solved by technology
Method used
Image
Examples
Embodiment 1
[0060] A treatment method for extracting vanadium tailings, the concrete steps are:
[0061] a) Agglomeration: adding 20% sodium carbonate, 8% coal powder and 1% bentonite to the vanadium extraction tailings to make pellets;
[0062] b) Reduction: Dry the above-mentioned green balls and carry out reduction roasting, the roasting temperature is 1100°C, and the roasting time is 60 minutes;
[0063] c) Grinding and leaching: take out the above-mentioned roasted ore for water quenching, place the obtained pulp in a wet ball mill for ball milling and leaching while it is hot, control the concentration of the pulp to 15-30%, the leaching temperature is 70°C, and the leaching time is 60 minutes;
[0064] d) Separation: filter and separate the above pulp to obtain vanadium leaching solution and leaching slag, and magnetically separate the leaching slag to obtain iron concentrate and tailings, with a magnetic field strength of 0.1-0.3T.
Embodiment 2
[0066] A treatment method for extracting vanadium tailings, the concrete steps are:
[0067] a) Agglomeration: adding 15% sodium hydroxide, 8% coal powder and 2% bentonite to the vanadium extraction tailings to make pellets;
[0068] b) Reduction: Dry the above-mentioned green balls and carry out reduction roasting, the roasting temperature is 1150°C, and the roasting time is 50 minutes;
[0069] c) Grinding and leaching: take out the above-mentioned roasted ore for water quenching, place the obtained pulp in a wet ball mill for ball milling and leaching while it is still hot, control the concentration of the pulp to 15-30%, the leaching temperature is 90°C, and the leaching time is 40 minutes;
[0070] d) Same as step d) of Example 1.
Embodiment 3
[0072] A treatment method for extracting vanadium tailings, the concrete steps are:
[0073] a) Agglomeration: adding 30% sodium sulfate, 10% coal powder and 0.5% bentonite to the vanadium extraction tailings to make pellets;
[0074] b) Reduction: Dry the above-mentioned green balls and carry out reduction roasting, the roasting temperature is 1200°C, and the roasting time is 45 minutes;
[0075] c) Grinding and leaching: take out the above-mentioned roasted ore for water quenching, place the obtained pulp in a wet ball mill for ball milling and leaching while it is still hot, control the concentration of the pulp to 15-30%, the leaching temperature is 65°C, and the leaching time is 55 minutes;
[0076] d) Same as step d) of Example 1.
PUM
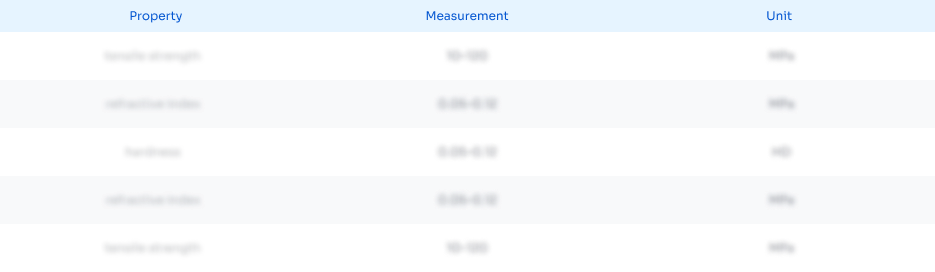
Abstract
Description
Claims
Application Information

- Generate Ideas
- Intellectual Property
- Life Sciences
- Materials
- Tech Scout
- Unparalleled Data Quality
- Higher Quality Content
- 60% Fewer Hallucinations
Browse by: Latest US Patents, China's latest patents, Technical Efficacy Thesaurus, Application Domain, Technology Topic, Popular Technical Reports.
© 2025 PatSnap. All rights reserved.Legal|Privacy policy|Modern Slavery Act Transparency Statement|Sitemap|About US| Contact US: help@patsnap.com