Conductive composite metal sheet between lugs in batteries or batteries and machining method
A processing method and metal sheet technology, which is applied to battery pack parts, circuits, electrical components, etc., can solve problems affecting battery pack performance, high welding requirements, and insufficient bonding strength of the alloy layer, etc.
- Summary
- Abstract
- Description
- Claims
- Application Information
AI Technical Summary
Problems solved by technology
Method used
Image
Examples
Embodiment 1
[0024] Embodiment 1, select the copper strip that is TP1, TP2, TU1 or TU2 for use, purity is the nickel strip of 99.5%, offer one deep 0.01um in the middle of the nickel strip, the groove of wide 1cm, the groove of copper strip corresponding nickel strip etc. The nickel and copper strips are cleaned with degreasing agent, and then the copper and nickel strips are respectively heated to 600 degrees Celsius and cooled naturally; the copper and nickel strips are cleaned and polished with polishing equipment made of steel wire wheels; Copper and nickel strips are compounded on a clad rolling mill; the clad strip is heated to 750 degrees Celsius, cooled naturally, and finally the clad copper-nickel strip is cold-rolled to the required thickness, and then annealed according to customer requirements.
Embodiment 2
[0025] Embodiment 2, select the copper strip that is TP1, TP2, TU1 or TU2 for use, purity is the nickel strip of 99.5%, offer one deep 0.9um in the middle of nickel strip, the groove of wide 8cm, the groove of copper strip corresponding nickel strip etc. Width cutting, nickel strips and copper strips are cleaned with degreasing agent, and then the copper strips and nickel strips are heated to 700 degrees Celsius and cooled naturally; the copper strips and nickel strips are cleaned and polished with polishing equipment made of steel wire wheels; Copper and nickel strips are compounded on a clad rolling mill; the clad strip is heated to 800 degrees Celsius, cooled naturally, and finally the clad copper-nickel strip is cold-rolled to the required thickness, and then annealed according to customer requirements.
[0026] In the above-mentioned embodiments, the composite surfaces of the copper strip and the nickel strip can be composited on one side or on both sides as required.
PUM
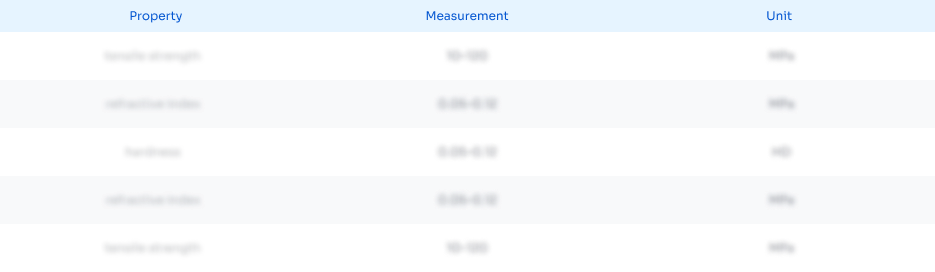
Abstract
Description
Claims
Application Information

- R&D Engineer
- R&D Manager
- IP Professional
- Industry Leading Data Capabilities
- Powerful AI technology
- Patent DNA Extraction
Browse by: Latest US Patents, China's latest patents, Technical Efficacy Thesaurus, Application Domain, Technology Topic, Popular Technical Reports.
© 2024 PatSnap. All rights reserved.Legal|Privacy policy|Modern Slavery Act Transparency Statement|Sitemap|About US| Contact US: help@patsnap.com