Ultrasonic testing method used for composite material foaming structures
A foam structure and composite material technology, which is applied in the analysis of solids using sonic/ultrasonic/infrasonic waves, can solve the problems of difficulty in detecting defects at the interface of foam bonding, low detection efficiency, and difficulty in determining defects.
- Summary
- Abstract
- Description
- Claims
- Application Information
AI Technical Summary
Problems solved by technology
Method used
Image
Examples
Embodiment 1
[0142] Choose the UPowr-1, UPower-2 and MUT-1 ultrasonic testing equipment produced by AVIC Composite Materials Co., Ltd. and the FJ-1 high-resolution ultrasonic transducer and high-energy transducer, respectively adopt water film coupling and high viscosity coupling The agent has carried out a series of practical testing applications on the overall foam structure of various composite materials. Among them, the size of the composite foam structure ranges from 100×500mm to 500×5000mm, and the thickness of the foam ranges from 20mm to 100mm.
[0143] Detection of Integral Foam Structure of Composite Materials
[0144] Place the overall foam structure of the composite material to be tested on the workbench, select the frequency of the transducer to be 1 MHz, and use MUT-1 ultrasonic testing equipment for detection, by moving the transmitting transducer 1 located on both sides of the overall foam structure of the composite material to be tested and receiving transducer 2, and ensu...
Embodiment 2
[0149] Choose the UPowr-1, UPower-2 and MUT-1 ultrasonic testing equipment produced by AVIC Composite Materials Co., Ltd. and the FJ-1 high-resolution ultrasonic transducer and high-energy transducer, respectively adopt water film coupling and high viscosity coupling The agent has carried out a series of practical testing applications on a variety of composite multilayer foam structures. Among them, the size of the composite multilayer foam structure ranges from 200×500mm to 500×5000mm, and the foam consists of two layers of foam glued together by adhesives. Made, the thickness of the foam ranges from 10mm-80mm,
[0150] Inspection of Multilayer Foam Structure of Composite Materials
[0151]Place the multi-layer foam structure of the composite material to be tested on the workbench, select the frequency of the transducer to be 0.5MHz, and use the MUT-1 ultrasonic testing equipment for detection. Transducer 1 and receiving transducer 2, and ensure that the transmitting transdu...
PUM
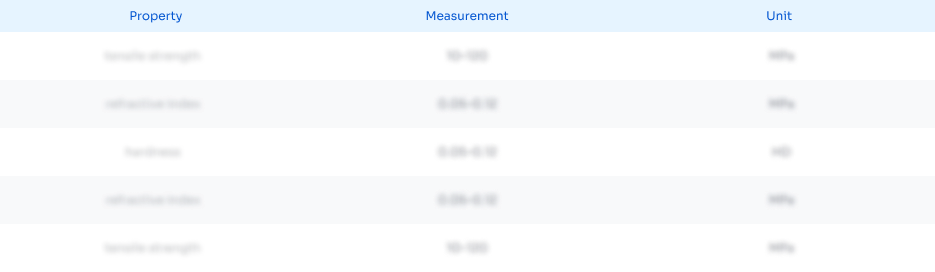
Abstract
Description
Claims
Application Information

- R&D
- Intellectual Property
- Life Sciences
- Materials
- Tech Scout
- Unparalleled Data Quality
- Higher Quality Content
- 60% Fewer Hallucinations
Browse by: Latest US Patents, China's latest patents, Technical Efficacy Thesaurus, Application Domain, Technology Topic, Popular Technical Reports.
© 2025 PatSnap. All rights reserved.Legal|Privacy policy|Modern Slavery Act Transparency Statement|Sitemap|About US| Contact US: help@patsnap.com