Method for testing contact rigidity of rock discontinuity structural plane, and apparatus thereof
A contact stiffness and structural surface technology, applied in the fields of geology and mechanics, can solve problems such as large errors, inability to measure the contact stiffness of large structural surfaces, and large disturbance of structural surfaces
- Summary
- Abstract
- Description
- Claims
- Application Information
AI Technical Summary
Problems solved by technology
Method used
Image
Examples
Embodiment 1
[0055] Test and analyze the normal contact stiffness and tangential contact stiffness of the limestone structural plane in an open-pit mine. The experimental process is as follows: figure 1 shown. Select an area with better outcropping on the structural surface 2, and use a brush to clean the structural surface 2 and the complete rock mass 1 on both sides to remove floating dust and loose broken bodies on the surface. Using gypsum, fix the vibration acceleration sensors 3 to 6 on the complete rock mass 1 on both sides of the structural surface 2 at a certain distance. The distances from acceleration sensors 4 and 5 to the structural surface 2 are both 5 cm, and the distances from acceleration sensors 3 and 6 to the structural surface are both 50 cm. Use the data line 7 to connect the acceleration sensors 3 to 6 to the acquisition instrument 8, and turn on the acquisition instrument 8 to make it in the sampling state. Select two hammering points, hammering point 9 and hammeri...
Embodiment 2
[0057] The normal contact stiffness and tangential contact stiffness were tested and analyzed for the granite structural surface exposed by the excavation of a certain slope. The experimental process is as follows: figure 2 shown. Clean up the two structural surfaces 2 exposed by the excavation and the surrounding complete rock mass 1 to remove surface impurities. Use expansion bolts to install the vibration velocity sensors 3, 4, 5, 6, 13, 14 to the corresponding positions of the complete rock mass 1 around the structural surface 2; and ensure that the sensors 3, 4, 5, 6, 13, 14 are on a straight line , and perpendicular to the structural plane 2. The distances from sensor 4 and sensor 5 to the left structural surface 2 are both 10 cm, and the distances from sensor 6 and sensor 13 to the right structural surface 2 are also 10 cm. Between sensor 3 and sensor 4, between sensor 5 and sensor 6, The distance between sensor 13 and sensor 14 is 5 m. The sensors 3, 4, 5, 6, 13, 1...
PUM
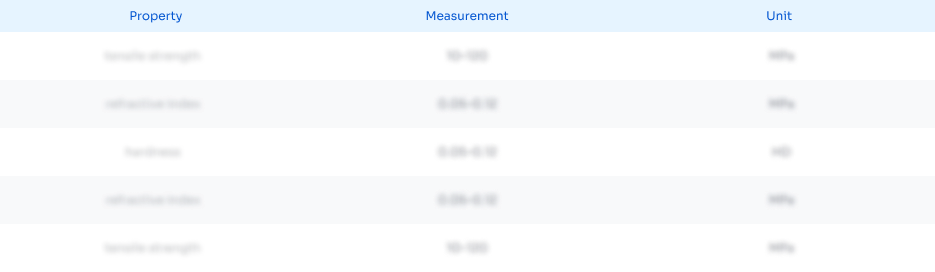
Abstract
Description
Claims
Application Information

- Generate Ideas
- Intellectual Property
- Life Sciences
- Materials
- Tech Scout
- Unparalleled Data Quality
- Higher Quality Content
- 60% Fewer Hallucinations
Browse by: Latest US Patents, China's latest patents, Technical Efficacy Thesaurus, Application Domain, Technology Topic, Popular Technical Reports.
© 2025 PatSnap. All rights reserved.Legal|Privacy policy|Modern Slavery Act Transparency Statement|Sitemap|About US| Contact US: help@patsnap.com