Coarse zinc smelting furnace
A smelting furnace and crude zinc technology, applied in the smelting field, can solve the problems of high production cost, large investment, difficult waste water treatment, etc., and achieve the effect of reducing emissions and ensuring smelting
- Summary
- Abstract
- Description
- Claims
- Application Information
AI Technical Summary
Problems solved by technology
Method used
Image
Examples
Embodiment Construction
[0014] The principles and features of the present invention are described below in conjunction with the accompanying drawings, and the examples given are only used to explain the present invention, and are not intended to limit the scope of the present invention.
[0015] Such as figure 1 As shown, a crude zinc smelting furnace includes a vertical furnace body 1, and the vertical furnace body 1 is provided with multi-layer combustion chambers 2, and each layer of combustion chambers 2 is provided with nozzles for injecting gas or air 3. A plurality of smelting pots 4 are arranged in the combustion chamber 2 of each layer, and the mouths of the smelting pots 4 are all arranged on the outer wall of the vertical furnace body 1, and inside the vertical furnace body 1 Two flues 5 are also provided, and the two flues 5 are respectively located at the two ends of the multi-layer combustion chamber 2, and the two flues 5 are all communicated with the two ends of the multi-layer combus...
PUM
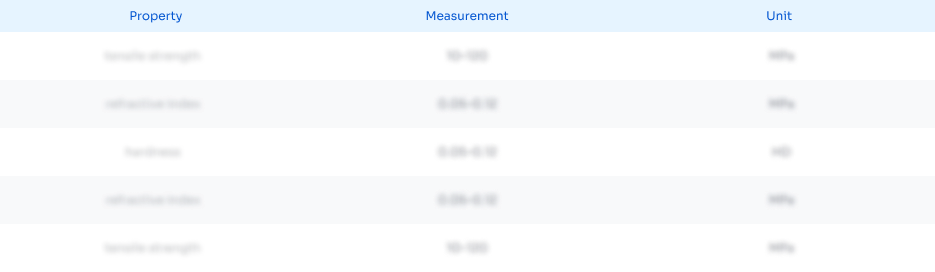
Abstract
Description
Claims
Application Information

- R&D
- Intellectual Property
- Life Sciences
- Materials
- Tech Scout
- Unparalleled Data Quality
- Higher Quality Content
- 60% Fewer Hallucinations
Browse by: Latest US Patents, China's latest patents, Technical Efficacy Thesaurus, Application Domain, Technology Topic, Popular Technical Reports.
© 2025 PatSnap. All rights reserved.Legal|Privacy policy|Modern Slavery Act Transparency Statement|Sitemap|About US| Contact US: help@patsnap.com