Gear machining and treating process
A technology for processing technology and gears, which is applied in the direction of metal material coating technology, coating, solid-state diffusion coating, etc., can solve problems such as waste, and achieve the goals of improving production efficiency, reducing the thickness of non-martensitic layers, and improving tissue performance Effect
- Summary
- Abstract
- Description
- Claims
- Application Information
AI Technical Summary
Problems solved by technology
Method used
Examples
Embodiment Construction
[0019] In order to make the object, technical solution and advantages of the present invention more clear, the present invention will be further described in detail below in conjunction with the examples.
[0020] The invention relates to a gear processing technology, comprising the following steps:
[0021] 1) Blanking and blank manufacturing: use forging or casting to process and manufacture gear blanks;
[0022] 2) Gear blank processing: process splines, keyways, and threads, and choose pulling, inserting, turning, and grinding methods for processing;
[0023] 3) Rough machining and semi-finishing of the tooth shape: According to the accuracy requirements, the tooth groove is cut out from the overall blank, and the corresponding finishing allowance is left on the groove side;
[0024] 4) Tooth end chamfering and deburring: the tooth end is trimmed into a certain shape as required, and the sharp edges and burrs on both sides of the tooth are removed at the same time;
[00...
PUM
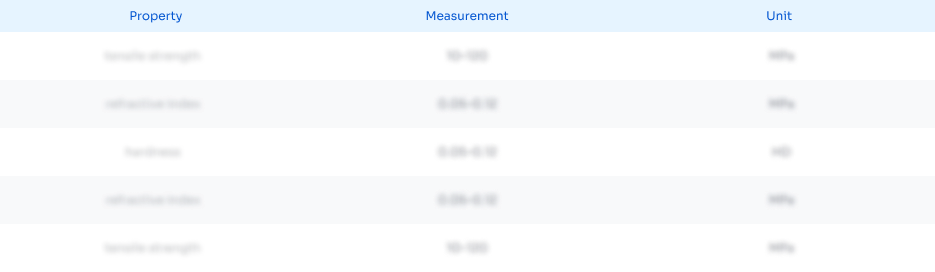
Abstract
Description
Claims
Application Information

- R&D Engineer
- R&D Manager
- IP Professional
- Industry Leading Data Capabilities
- Powerful AI technology
- Patent DNA Extraction
Browse by: Latest US Patents, China's latest patents, Technical Efficacy Thesaurus, Application Domain, Technology Topic, Popular Technical Reports.
© 2024 PatSnap. All rights reserved.Legal|Privacy policy|Modern Slavery Act Transparency Statement|Sitemap|About US| Contact US: help@patsnap.com