Zircon aluminum silicate glass and preparation method thereof
A zirconium aluminosilicate and glass technology, applied in glass manufacturing equipment, glass tempering, manufacturing tools, etc., can solve the problems of application limitation, reduce the life of furnace refractory materials, and high energy consumption, and achieve less bubble defects, The best clarifying effect and the effect of low melting temperature
- Summary
- Abstract
- Description
- Claims
- Application Information
AI Technical Summary
Problems solved by technology
Method used
Image
Examples
preparation example Construction
[0048] The above-mentioned zirconium aluminosilicate glass is prepared by a float process. see figure 1 , the preparation method of the above-mentioned zirconium aluminosilicate glass comprises the following steps:
[0049] Step S110: Quartz sand, Na 2 CO3 , CaCO 3 、KNO 3 、K 2 CO 3 、NaNO 3 , MgO, Al 2 o 3 , CeO 2 , SnO 2 , zircon sand, TiO 2 Mix with glass clarifier to obtain a mixture, keep the mixture at 1400℃~1520℃ for 1 hour to melt the mixture, wherein the glass clarifier includes NH 4 NO 3 、Na 2 SO 4 , CeO 2 and SnO 2 .
[0050] The ratio of the above raw materials makes the final zirconium aluminosilicate glass include the following components in terms of mass percentage: SiO 2 55.0~68.0%; Al 2 o 3 5.0~20.0%; CaO 0~5.0%; MgO 0~10.0%; K 2 O1.0~8.0%; Na 2 O 10.0~17.0%; CeO 2 0.01~2.0%;TiO 2 0.001~2.0%; ZrO 2 0.3~3.0%; SnO 2 0.01~1.5% and Fe 2 o 3 0.010-0.012%. Among them, K 2 O and Na 2 The total mass percentage of O is 12.0-20.0%, and K 2 ...
Embodiment 1
[0069] 1. Quartz sand, Na 2 CO 3 、KNO 3 、K 2 CO 3 、NaNO 3 , MgO, Al 2 o 3 , CeO 2 , SnO 2 , zircon sand, TiO 2 Mix with a glass clarifier to obtain a mixture, place the mixture in an electric furnace, and keep it warm at 1500°C for 1 hour to melt the mixture, wherein the glass clarifier includes NH 4 NO 3 、Na 2 SO 4 , CeO 2 and SnO 2 ;
[0070] 2. Heat up the melted mixture to 1605°C for clarification for 2 hours to obtain molten glass;
[0071] 3. The molten glass is formed by the float method to obtain zirconium aluminosilicate glass. The components of the zirconium aluminosilicate glass are shown in Table 1;
[0072] 4. Heat the zirconium aluminosilicate glass at 300°C for 30 minutes, then place it in a potassium nitrate melt at 420°C for 6 hours, and finally cool it down to 100°C at a rate of 5°C / min, and Heat preservation at 100° C. for 30 minutes to obtain tempered zirconium aluminosilicate glass.
Embodiment 2
[0074] 1. Quartz sand, Na 2 CO 3 、KNO 3 、K 2 CO 3 、NaNO 3 , MgO, Al 2 o 3 , CeO 2 , SnO 2 , zircon sand, TiO 2 Mix with a glass clarifier to obtain a mixture, place the mixture in an electric furnace, and keep it warm at 1510°C for 1 hour to melt the mixture, wherein the glass clarifier includes NH 4 NO 3 、Na 2 SO 4 , CeO 2 and SnO 2 ;
[0075] 2. Heat the melted mixture to 1615°C for clarification for 2 hours to obtain molten glass;
[0076] 3. The molten glass is formed by the float method to obtain zirconium aluminosilicate glass. The components of the zirconium aluminosilicate glass are shown in Table 1;
[0077] 4. Heat the zirconium aluminosilicate glass at 300°C for 30 minutes, then place it in a potassium nitrate melt at 420°C for 6 hours, and finally cool it down to 100°C at a rate of 5°C / min, and Heat preservation at 100° C. for 30 minutes to obtain tempered zirconium aluminosilicate glass.
PUM
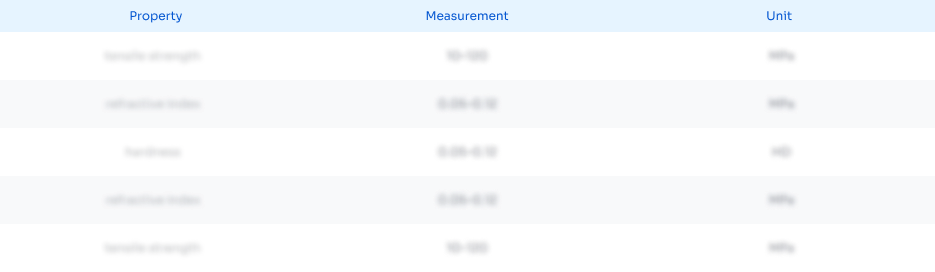
Abstract
Description
Claims
Application Information

- Generate Ideas
- Intellectual Property
- Life Sciences
- Materials
- Tech Scout
- Unparalleled Data Quality
- Higher Quality Content
- 60% Fewer Hallucinations
Browse by: Latest US Patents, China's latest patents, Technical Efficacy Thesaurus, Application Domain, Technology Topic, Popular Technical Reports.
© 2025 PatSnap. All rights reserved.Legal|Privacy policy|Modern Slavery Act Transparency Statement|Sitemap|About US| Contact US: help@patsnap.com