A method for controlling the purity of heavy rail steel
A pure, heavy-gauge steel technology, applied in the manufacture of converters, etc., can solve the problems of low desulfurization efficiency and no consideration of inclusions, etc., and achieve high desulfurization efficiency, desulfurization efficiency and stable effects
- Summary
- Abstract
- Description
- Claims
- Application Information
AI Technical Summary
Problems solved by technology
Method used
Examples
Embodiment 1
[0046] A, converter smelting
[0047] The molten iron entering the converter has an S content of 0.016%. After the converter smelting is completed, the steel is tapped. During the tapping process, a silicon-calcium-barium alloy is added to the ladle for deoxidation. The amount added is 2.5kg of silicon-calcium-barium and silicon-calcium After the addition of barium is completed, other alloys required by the steel grade are added immediately, and at the same time, active lime is added to the ladle to add 5kg per ton of molten steel. After tapping, evenly add calcium carbide to the ladle slag surface to add 0.2kg per ton of molten steel. In the above-mentioned tapping process, the flow rate of argon blowing at the bottom of the ladle is 60NLl / min. After tapping, blow argon for 6 minutes with a bottom blowing argon flow rate of 50NL / min, and then send the molten steel to LF for refining.
[0048] B, LF furnace refining
[0049] After the molten steel arrives at the LF station,...
Embodiment 2
[0056] A, converter smelting
[0057] The molten iron entering the converter has an S content of 0.020%. After the converter smelting is completed, the steel is tapped. During the tapping process, a silicon-calcium-barium alloy is added to the ladle for deoxidation. The amount of addition is 3.5kg per ton of molten steel. Immediately after the addition is completed, other alloys required by the steel grade are added. At the same time, add 5kg of active lime per ton of molten steel to the ladle. After tapping, 0.4kg of calcium carbide per ton of molten steel is evenly added to the ladle slag surface. In the above tapping process, the argon gas flow rate of ladle bottom blowing is 60NL / min. After tapping, blow argon for 6 minutes with a bottom blowing argon flow rate of 50NL / min, and then send the molten steel to LF for refining.
[0058] B, LF furnace refining
[0059] After the molten steel reaches the LF station, turn on the bottom blowing argon to blow the argon at the b...
Embodiment 3
[0066] A, converter smelting
[0067] The molten iron entering the converter has an S content of 0.010%. After the converter smelting is completed, the steel begins to be tapped. During the tapping process, a silicon-calcium-barium alloy is added to the ladle for deoxidation. The amount of addition is 3.0kg per ton of molten steel. Then add other alloys required by the steel grade. At the same time, add 3kg of active lime per ton of molten steel to the ladle. After tapping, 0.3 kg of calcium carbide per ton of molten steel is evenly added to the slag surface of the ladle. In the above tapping process, the argon gas flow rate of ladle bottom blowing is 60NL / min. After tapping, blow argon for 6 minutes with a bottom blowing argon flow rate of 50NL / min, and then send the molten steel to LF for refining.
[0068] B, LF furnace refining
[0069] After the molten steel reaches the LF station, turn on the bottom blowing argon to blow the argon at the bottom of the ladle. The flow...
PUM
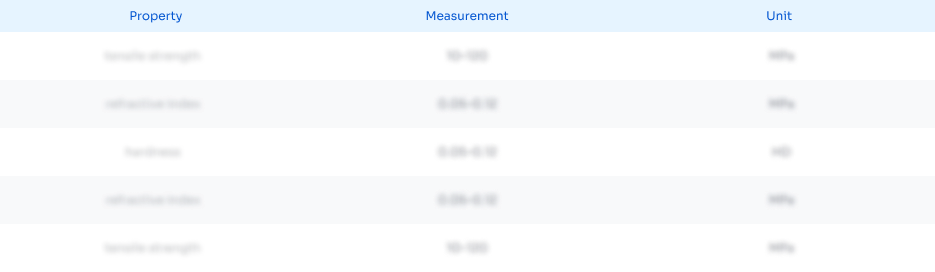
Abstract
Description
Claims
Application Information

- Generate Ideas
- Intellectual Property
- Life Sciences
- Materials
- Tech Scout
- Unparalleled Data Quality
- Higher Quality Content
- 60% Fewer Hallucinations
Browse by: Latest US Patents, China's latest patents, Technical Efficacy Thesaurus, Application Domain, Technology Topic, Popular Technical Reports.
© 2025 PatSnap. All rights reserved.Legal|Privacy policy|Modern Slavery Act Transparency Statement|Sitemap|About US| Contact US: help@patsnap.com