Preparation method of paper-surface gypsum board
A paper-faced gypsum board and gypsum clinker technology, applied in the field of paper-faced gypsum board preparation, can solve the problems of limited bonding performance of cover paper and unguaranteed bonding quality, so as to improve the bonding quality of boards and reduce the Dependent, high-return effects
- Summary
- Abstract
- Description
- Claims
- Application Information
AI Technical Summary
Problems solved by technology
Method used
Image
Examples
Embodiment Construction
[0023] The specific implementation of a resource-intensive high-performance gypsum board preparation method disclosed by the present invention will be described in detail below in conjunction with the accompanying drawings, which is not intended to limit the scope of the present invention.
[0024] 1. Raw material types and proportioning scheme:
[0025] (1) Types and functions of raw materials:
[0026] 1. Gypsum clinker: desulfurized gypsum is calcined in a hammer disperser, dispersed in the air under the action of the rotating hammer head, and all attached water and part of crystal water are removed to produce plaster powder with hemihydrate gypsum as the main component , Gypsum powder enters the ball mill for grinding and modification to obtain gypsum clinker. The gypsum clinker has the characteristics of hydration and hardening of cementitious materials.
[0027] 2. Water: necessary material for hydration of gypsum clinker.
[0028] 3. PGCS: Jianjie construction grade p...
PUM
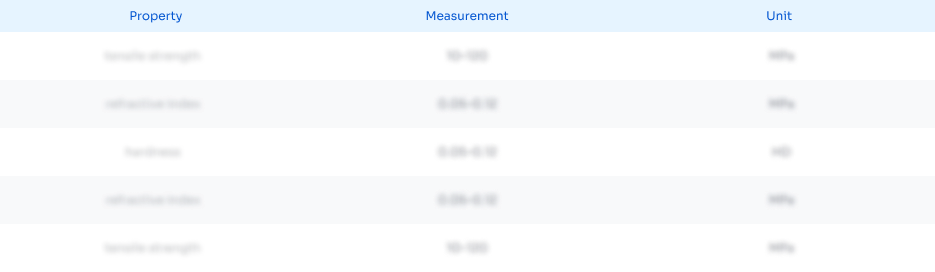
Abstract
Description
Claims
Application Information

- R&D
- Intellectual Property
- Life Sciences
- Materials
- Tech Scout
- Unparalleled Data Quality
- Higher Quality Content
- 60% Fewer Hallucinations
Browse by: Latest US Patents, China's latest patents, Technical Efficacy Thesaurus, Application Domain, Technology Topic, Popular Technical Reports.
© 2025 PatSnap. All rights reserved.Legal|Privacy policy|Modern Slavery Act Transparency Statement|Sitemap|About US| Contact US: help@patsnap.com