Sheet metal bending system and method with angle regulating and controlling function and phased bending function
A technology of stages and angles, applied in metal processing, metal processing equipment, feeding devices, etc., can solve problems such as poor effect, long processing cycle, and inability to adjust, so as to save subsequent processing processes, remove burrs and cracks, and improve The effect of processing quality
- Summary
- Abstract
- Description
- Claims
- Application Information
AI Technical Summary
Problems solved by technology
Method used
Image
Examples
Embodiment Construction
[0026] The specific implementation manner of the present invention will be described below in conjunction with the accompanying drawings.
[0027] Such as Figure 1 to Figure 4 As shown, the sheet metal bending system with angle control and stage bending in this embodiment includes a drive motor 3 installed on the frame 1, a clamping and fixing seat 2 and a host 4 that controls the drive motor 3, and the drive motor 3 The bending shaft 6 is installed on the motor shaft, and the workpiece 5 is installed on the clamping seat 2;
[0028] It also includes an ultrasonic thickness detector 8 installed on the frame 1 by means of a first bracket 7, a first pressure sensor 12 and a roller 15 installed on the clamping and fixing seat 2, a detection feedback device and a controller connected to the host 4 10. The roller 15 is located on the bending side of the workpiece 5, and the first pressure sensor 12 is installed in the installation groove 21 of the clamping seat 2, and the pressur...
PUM
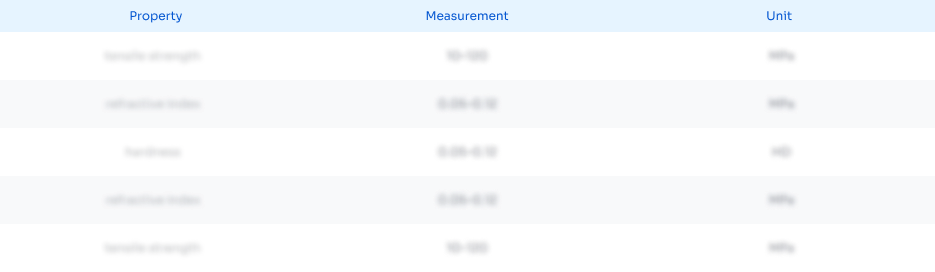
Abstract
Description
Claims
Application Information

- Generate Ideas
- Intellectual Property
- Life Sciences
- Materials
- Tech Scout
- Unparalleled Data Quality
- Higher Quality Content
- 60% Fewer Hallucinations
Browse by: Latest US Patents, China's latest patents, Technical Efficacy Thesaurus, Application Domain, Technology Topic, Popular Technical Reports.
© 2025 PatSnap. All rights reserved.Legal|Privacy policy|Modern Slavery Act Transparency Statement|Sitemap|About US| Contact US: help@patsnap.com