A kind of silicon-based composite material, its preparation method and application
A silicon-based composite material and a technology for silicon-based materials, applied in the field of lithium-ion batteries, can solve the problems of restricting the commercial application of lithium-ion batteries, deteriorating cycle performance of lithium-ion batteries, and changing the volume of active material particles, etc. Industrial production, simple and easy implementation cost, the effect of improving energy density
- Summary
- Abstract
- Description
- Claims
- Application Information
AI Technical Summary
Problems solved by technology
Method used
Image
Examples
Embodiment 1
[0062] Preparation of silicon-based composite material A1:
[0063] 100 parts by mass of SiOx powder were dispersed in 1000 parts by mass of 3-aminopropyltriethoxysilane in an anhydrous tetrahydrofuran solution with a concentration of 1 mol / L. Add 0.1 parts by mass of dibutyltin acetate and 1 part by mass of water to the resulting suspension under constant stirring, and react at 20°C for 5 hours, then filter and collect the solids at 500°C for 3 hours to obtain The silicon-based composite material is denoted as A1.
[0064] Production of negative electrode sheet N1:
[0065] Dissolve 5 parts by mass of polyacrylic acid (abbreviated as PAA) in 110 parts by mass of water, add the obtained A1 and 5 parts by mass of conductive agent acetylene black, and mix uniformly to obtain negative electrode slurry. The negative electrode slurry is evenly coated on the negative electrode current collector copper foil with a thickness of 12 μm, and the solid coating amount is 0.0089 g / cm ...
Embodiment 2
[0073] Preparation of silicon-based composite material A2:
[0074] 100 parts by mass of SiOx powder were dispersed in 500 parts by mass of p-anilinotriisopropoxysilane in anhydrous dichloromethane solution with a concentration of 1.2 mol / L. The resulting suspension was heated to 40°C under constant stirring, 1 mass part of pyridine and 5 mass parts of water were added, and after reacting at 40°C for 7 hours, the solid collected by spray drying was treated at 300°C After 5 hours, the silicon-based composite material was obtained, denoted as A2.
[0075] Production of negative electrode sheet N2:
[0076] Dissolve 5 parts by mass of polyacrylic acid (abbreviated as PAA) in 110 parts by mass of water, add the obtained A2 and 5 parts by mass of conductive agent acetylene black, and mix uniformly to obtain negative electrode slurry. The negative electrode slurry is evenly coated on the negative electrode current collector copper foil with a thickness of 12 μm, and the solid ...
Embodiment 3
[0080] Preparation of silicon-based composite material A3:
[0081] 100 parts by mass of SiOx powder were dispersed in 1000 parts by mass of a toluene solution having a p-anilinotriisopropoxysilane concentration of 2 mol / L, and 10 parts by mass of water was added. The resulting suspension was heated to 90°C under constant stirring, and after reacting at 90°C for 10 hours, the solid collected by spray drying was treated at 100°C for 15 hours to obtain the silicon-based composite material, recorded as for A3.
[0082] Production of negative electrode sheet N3:
[0083] Dissolve 5 parts by mass of polymethyl methacrylate (abbreviated as PMAA) in 110 parts by mass of water, add the obtained A3 and 5 parts by mass of conductive agent acetylene black, and mix uniformly to obtain negative electrode slurry. The negative electrode slurry is evenly coated on the negative electrode current collector copper foil with a thickness of 12 μm, and the solid coating amount is 0.0089 g / cm ...
PUM
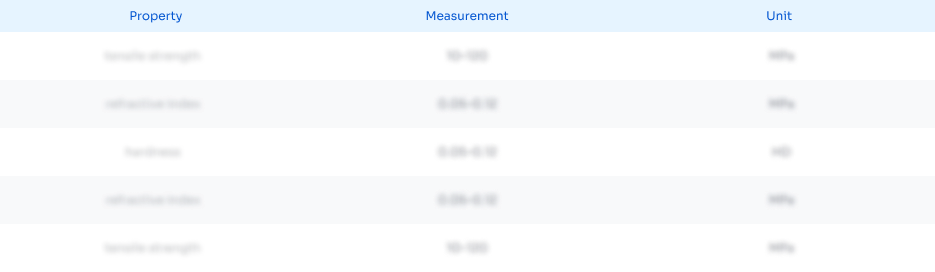
Abstract
Description
Claims
Application Information

- R&D
- Intellectual Property
- Life Sciences
- Materials
- Tech Scout
- Unparalleled Data Quality
- Higher Quality Content
- 60% Fewer Hallucinations
Browse by: Latest US Patents, China's latest patents, Technical Efficacy Thesaurus, Application Domain, Technology Topic, Popular Technical Reports.
© 2025 PatSnap. All rights reserved.Legal|Privacy policy|Modern Slavery Act Transparency Statement|Sitemap|About US| Contact US: help@patsnap.com