tft substrate group and its manufacturing method
A manufacturing method and a technology for a substrate set, which are applied in the manufacture of semiconductor/solid-state devices, electrical components, and electrical solid-state devices, etc., can solve the problems of increasing the consumption of etching solution, endless etching, and increasing the cost of copper manufacturing processes, and reduce endless etching. risk, improve product quality, and improve the effect of endless etching
- Summary
- Abstract
- Description
- Claims
- Application Information
AI Technical Summary
Problems solved by technology
Method used
Image
Examples
Embodiment Construction
[0039] In order to further illustrate the technical means adopted by the present invention and its effects, the following describes in detail in conjunction with preferred embodiments of the present invention and accompanying drawings.
[0040] see Figure 4-5 , the present invention firstly provides a TFT substrate group, comprising: several TFT substrates 20, and a spacer area 30 between several TFT substrates 20 to separate the several TFT substrates 20, the TFT substrate 20 is provided with metal The electrode 21 is provided with a metal pattern 31 spaced from the metal electrode 21 in the spaced area 30 .
[0041] Specifically, the material of the metal electrode 21 and the metal pattern 31 is copper.
[0042] Wherein, the plurality of TFT substrates 20 are arranged in a matrix in the TFT substrate group.
[0043] The spacer regions 30 are distributed in grid form in the TFT substrate group.
[0044] Specifically, the shape of the metal electrode 21 is a rectangle.
[0...
PUM
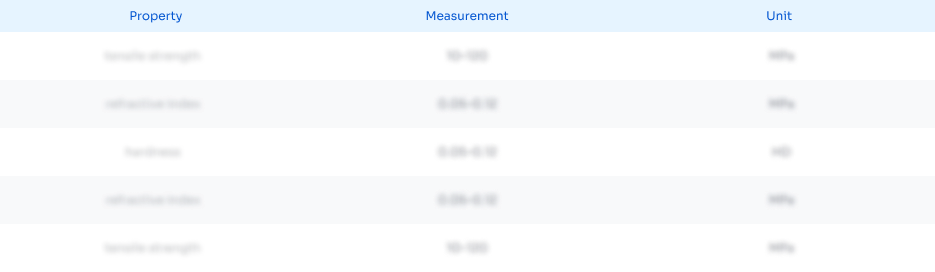
Abstract
Description
Claims
Application Information

- R&D
- Intellectual Property
- Life Sciences
- Materials
- Tech Scout
- Unparalleled Data Quality
- Higher Quality Content
- 60% Fewer Hallucinations
Browse by: Latest US Patents, China's latest patents, Technical Efficacy Thesaurus, Application Domain, Technology Topic, Popular Technical Reports.
© 2025 PatSnap. All rights reserved.Legal|Privacy policy|Modern Slavery Act Transparency Statement|Sitemap|About US| Contact US: help@patsnap.com