Wear-resistant paper-plastic composite bag and preparation method for same
A paper-plastic composite bag, wear-resistant technology, applied in the field of paper-plastic bag manufacturing, can solve problems such as cracking, affecting the normal use of paper-plastic bags, and wrinkling of the plastic layer, achieving excellent wear resistance and suitable for large-scale production , the effect of mild reaction conditions
- Summary
- Abstract
- Description
- Claims
- Application Information
AI Technical Summary
Problems solved by technology
Method used
Examples
preparation example Construction
[0026] The present invention also provides a method for preparing a wear-resistant paper-plastic composite bag, the method comprising:
[0027] (1) Polypropylene, polyethylene, epoxy resin, ultra-high molecular weight polyethylene, silicone, phenolic resin, glass fiber, polytetrafluoroethylene, molybdenum disulfide, glycerin, dimethyl phthalate and hard Sodium bicarbonate is mixed and then extruded to form a film;
[0028] (2) The film is heated and coated on the surface of the paper layer to form a plastic layer to make a composite paper; or the film is cut, drawn and woven into a plastic layer, and then the plastic layer is glued Adhesive is stuck on the surface of described paper layer to make composite paper;
[0029] (3) Processing the composite paper into a wear-resistant paper-plastic composite bag.
[0030] In the above-mentioned preparation method, the weight-average molecular weight of polypropylene can be selected in a wide range, but from the consideration of imp...
Embodiment 1
[0042] (1) At 25°C, polypropylene (weight average molecular weight is 90000), polyethylene (weight average molecular weight is 18000), epoxy resin (weight average molecular weight is 6000), ultra-high molecular weight polyethylene (weight average molecular weight is 1600000), silicone (weight average molecular weight 18000), phenolic resin (weight average molecular weight 15000), glass fiber, polytetrafluoroethylene (weight average molecular weight 25000), molybdenum disulfide, glycerin, dimethyl phthalate Ester and sodium stearate (the mass ratio of raw materials is 100:12:25:18:14:17:10:16:13:2:3:4) were mixed for 2 hours, and extruded at 210°C to obtain film;
[0043] (2) Heating the film to 230°C and coating it on the surface of the paper layer to form a plastic layer to make a composite paper (the thickness ratio of the paper layer to the plastic layer is 1:1);
[0044] (3) Process the above-mentioned composite paper into a wear-resistant paper-plastic composite bag A1. ...
Embodiment 2
[0046] (1) At 25°C, polypropylene (weight average molecular weight is 80000), polyethylene (weight average molecular weight is 14000), epoxy resin (weight average molecular weight is 4000), ultra-high molecular weight polyethylene (weight average molecular weight is 1500000), silicone (weight average molecular weight 15000), phenolic resin (weight average molecular weight 12000), glass fiber, polytetrafluoroethylene (weight average molecular weight 20000), molybdenum disulfide, glycerin, dimethyl phthalate Ester and sodium stearate (the mass ratio of raw materials is 100:10:25:18:14:17:10:16:13:1:2:1) were mixed for 2 hours, and extruded at 210°C to obtain film;
[0047] (2) heating the film to 230° C. and coating it on the surface of the paper layer to form a plastic layer to make a composite paper (the thickness ratio of the paper layer to the plastic layer is 1.05:1);
[0048] (3) Process the above-mentioned composite paper into a wear-resistant paper-plastic composite bag...
PUM
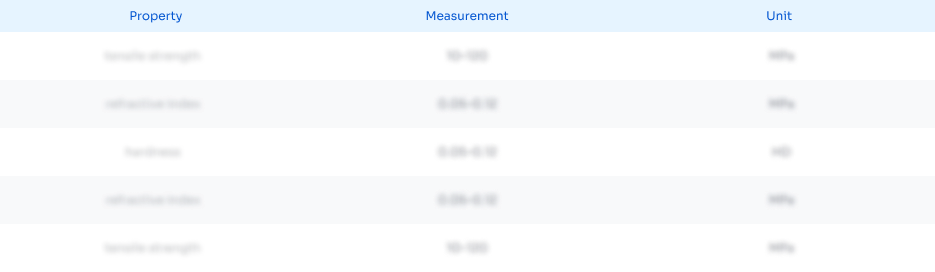
Abstract
Description
Claims
Application Information

- Generate Ideas
- Intellectual Property
- Life Sciences
- Materials
- Tech Scout
- Unparalleled Data Quality
- Higher Quality Content
- 60% Fewer Hallucinations
Browse by: Latest US Patents, China's latest patents, Technical Efficacy Thesaurus, Application Domain, Technology Topic, Popular Technical Reports.
© 2025 PatSnap. All rights reserved.Legal|Privacy policy|Modern Slavery Act Transparency Statement|Sitemap|About US| Contact US: help@patsnap.com