Basic etching back-polishing process for crystalline silicon battery
A crystalline silicon battery, alkaline technology, applied in the direction of circuits, electrical components, sustainable manufacturing/processing, etc., can solve the problems of unfavorable weak light effect, high leakage ratio, damage to p-n, etc., to avoid surface defects and low leakage ratio , does not cause the effect of increasing square resistance
- Summary
- Abstract
- Description
- Claims
- Application Information
AI Technical Summary
Problems solved by technology
Method used
Image
Examples
Embodiment
[0027] An alkaline etching back-throwing process for a crystalline silicon battery comprises the following specific steps:
[0028] 1) Use the nozzle to spray water on the front of the silicon wafer to protect the PSG layer on the front of the silicon wafer; due to the protection of the PSG layer on the front of the silicon wafer, the acid mist cannot directly corrode the P-N junction, making the square resistance stable.
[0029] 2) Use HF solution to remove the PSG layer on the back of the silicon wafer by means of capillary rollers; due to the protection of the water film, the PSG layer on the front of the silicon wafer will not be removed;
[0030] 3) Clean the residual HF solution on the silicon wafer in the water tank; prevent the HF solution from being brought into the alkali tank, and neutralize the alkali in the alkali tank;
[0031] 4) Dry the surface of the silicon wafer through a hot air knife with a temperature of 50-70°C; prevent water from being brought into the...
PUM
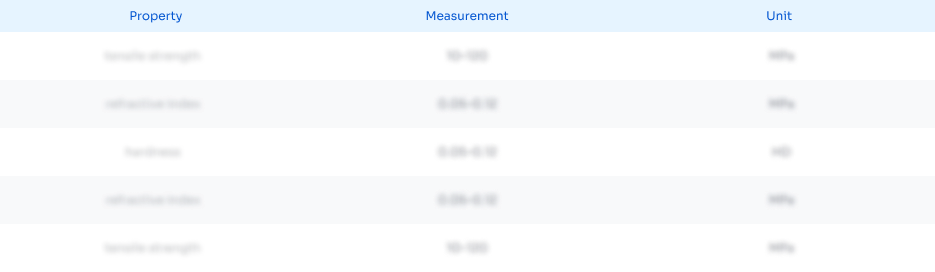
Abstract
Description
Claims
Application Information

- R&D
- Intellectual Property
- Life Sciences
- Materials
- Tech Scout
- Unparalleled Data Quality
- Higher Quality Content
- 60% Fewer Hallucinations
Browse by: Latest US Patents, China's latest patents, Technical Efficacy Thesaurus, Application Domain, Technology Topic, Popular Technical Reports.
© 2025 PatSnap. All rights reserved.Legal|Privacy policy|Modern Slavery Act Transparency Statement|Sitemap|About US| Contact US: help@patsnap.com