Production method of low-titanium bearing steel GCr15
A production method and technology of bearing steel, which is applied in the field of bearing steel preparation, can solve the problems of increased cost, low yield, difficulty in controlling the oxidation of ferrochrome alloy, etc., and achieve the effect of solving cost increase and saving precious ferroalloy
- Summary
- Abstract
- Description
- Claims
- Application Information
AI Technical Summary
Problems solved by technology
Method used
Examples
Embodiment 1
[0019] A production method of low-titanium bearing steel GCr15, sequentially through EBT eccentric bottom electric furnace, LF refining furnace, VD vacuum furnace, continuous casting or mold casting, specifically comprises the following steps:
[0020] 1) To charge the EBT eccentric bottom electric furnace, according to the weight percentage, the proportion of molten iron is 60%, and the rest is mixed with scrap steel; what adopts in this embodiment is that the molten steel can be the high-quality molten iron+scrap steel of Benxi Iron and Steel, and the scrap steel here refers to , the standard number is steel scrap stipulated in GB 4223;
[0021] 2) The electric furnace blows oxygen into the molten steel through a supersonic oxygen lance to remove C, control the tapping C≤0.40% (weight percentage), and tap the steel at a temperature of 1640°C. The eccentric bottom tapping is adopted to prevent under-oxidation by leaving steel and slag. Slag, while tapping the steel, add high-...
Embodiment 2
[0027] The difference from Example 1 is a production method of low-titanium bearing steel GCr15, which sequentially passes through EBT eccentric bottom electric furnace, LF refining furnace, VD vacuum furnace, continuous casting or die casting, specifically including the following steps:
[0028] 1) To charge the EBT eccentric bottom electric furnace, according to the weight percentage, the proportion of molten iron is 70%, and the rest is mixed with scrap steel;
[0029] 2) The electric furnace blows oxygen into the molten steel through a supersonic oxygen lance to remove C, and controls the tapping C≤0.40%, and the tapping temperature is 1685°C. The eccentric bottom tapping is adopted to prevent the oxidized slag by leaving steel and slag. At the same time as the steel is tapped, high-carbon ferrochromium, silicon-manganese alloy and ferrosilicon are respectively added according to the weight percentage content of Cr 1.40%, Mn 0.25% and Si 0.15%;
[0030] 3) After tapping, e...
PUM
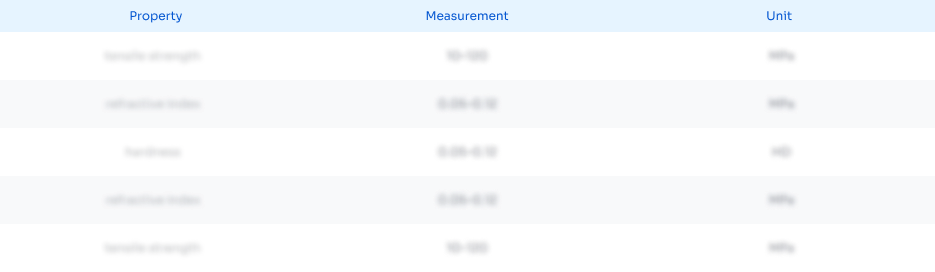
Abstract
Description
Claims
Application Information

- Generate Ideas
- Intellectual Property
- Life Sciences
- Materials
- Tech Scout
- Unparalleled Data Quality
- Higher Quality Content
- 60% Fewer Hallucinations
Browse by: Latest US Patents, China's latest patents, Technical Efficacy Thesaurus, Application Domain, Technology Topic, Popular Technical Reports.
© 2025 PatSnap. All rights reserved.Legal|Privacy policy|Modern Slavery Act Transparency Statement|Sitemap|About US| Contact US: help@patsnap.com