A combined treatment method for sodium fluorosilicate production and magnesium removal from phosphate rock
A sodium fluorosilicate and combined treatment technology, which is applied in the treatment of phosphate materials, silicon halide compounds, magnesium hydroxide, etc., can solve the problems of large loss of phosphorus pentoxide, strong corrosion of mixed acids, and high equipment requirements. Effects of reducing pollution, improving grade, and reducing environmental pollution
- Summary
- Abstract
- Description
- Claims
- Application Information
AI Technical Summary
Problems solved by technology
Method used
Image
Examples
Embodiment 1
[0031] A combined treatment method for the production of sodium fluorosilicate and the removal of magnesium from phosphate ore. The sewage discharged from the production process of sodium fluorosilicate is added dropwise to the slurry of phosphate ore. The pH value in the kettle is kept constant at 0.5. After the phosphate rock slurry in the reactor has reacted for 2 hours, the reaction slurry in the reactor is subjected to liquid-solid separation treatment to obtain filter cake and filtrate, and the filter cake is washed with water for 2 hours. times and dried to obtain phosphate concentrate; the washing liquid is returned to the phosphate rock slurry preparation step, and the filtrate is used for the preparation of magnesium-containing by-products.
[0032] Specifically include the following steps:
[0033] (1) Put the phosphate rock in a pulverizer to pulverize and sieve, and control the pulverized phosphate rock powder. 80% of the mineral powder can pass through a 100-mesh...
Embodiment 2
[0042] A combined treatment method for the production of sodium fluorosilicate and the removal of magnesium from phosphate ore. The sewage discharged from the production process of sodium fluorosilicate is added dropwise to the slurry of phosphate ore. The pH value in the kettle is kept constant at 4. After the phosphate rock slurry in the reactor has reacted for 4 hours, the reaction slurry in the reactor is subjected to liquid-solid separation treatment to obtain filter cake and filtrate, and the filter cake is washed with water for 3 hours. times and dried to obtain phosphate concentrate; the washing liquid is returned to the phosphate rock slurry preparation step, and the filtrate is used for the preparation of magnesium-containing by-products.
[0043] Specifically include the following steps:
[0044] (1) Put the phosphate rock in a pulverizer to pulverize and sieve, and control the pulverized phosphate rock powder. 80% of the mineral powder can pass through a 100-mesh s...
Embodiment 3
[0055] A combined treatment method for the production of sodium fluorosilicate and the removal of magnesium from phosphate ore. The sewage discharged from the production process of sodium fluorosilicate is added dropwise to the slurry of phosphate ore. The pH value in the kettle is kept constant at 2. After the phosphate rock slurry in the reactor has reacted for 3 hours, the reaction slurry in the reactor is subjected to liquid-solid separation treatment to obtain filter cake and filtrate, and the filter cake is washed with water for 2.5 times and dried to obtain phosphate concentrate; the washing liquid is returned to the phosphate rock slurry preparation step, and the filtrate is used for the preparation of magnesium-containing by-products.
[0056] Specifically include the following steps:
[0057] (1) Put the phosphate rock in a pulverizer to pulverize and sieve, and control the pulverized phosphate rock powder. 80% of the mineral powder can pass through a 100-mesh sieve,...
PUM
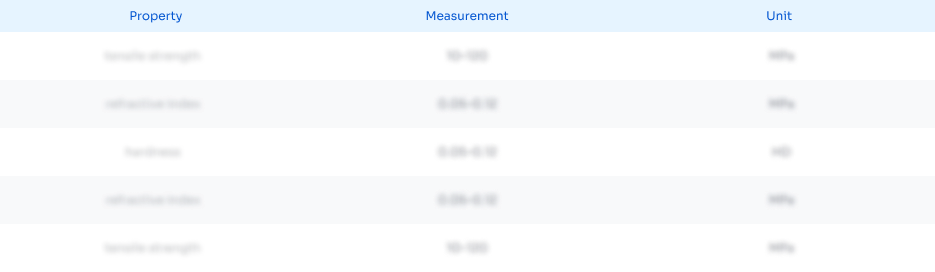
Abstract
Description
Claims
Application Information

- R&D
- Intellectual Property
- Life Sciences
- Materials
- Tech Scout
- Unparalleled Data Quality
- Higher Quality Content
- 60% Fewer Hallucinations
Browse by: Latest US Patents, China's latest patents, Technical Efficacy Thesaurus, Application Domain, Technology Topic, Popular Technical Reports.
© 2025 PatSnap. All rights reserved.Legal|Privacy policy|Modern Slavery Act Transparency Statement|Sitemap|About US| Contact US: help@patsnap.com