Rock-peeling gangue dry-process desliming method
A technology of stripping rock tailings and desliming, which is applied in the field of resource utilization of solid waste, which can solve the problems of lack of water mining areas, drainage, and difficulty in water washing, so as to reduce the washing water of gravel, save water resources, and reduce soil waste. residual effect
- Summary
- Abstract
- Description
- Claims
- Application Information
AI Technical Summary
Problems solved by technology
Method used
Image
Examples
Embodiment 1
[0033] The total amount of crushed stones and tailings produced during the mining and processing of rock tailings in the early stage is about 8:1 (soil content 11.1%). The total amount of gravel is about 900 tons, of which the total amount of soil is about 100 tons, and a total of 10 tons of desliming agent is added according to the proportion of 10% of the total amount of soil in the excavation tailings area;
[0034] Use an excavator to dig a large pit of 3m×3m×1m in the center of the tailings excavation area, add 10 tons of deslimer to it, and then use a forklift and excavator to excavate the tailings The tailings in the area are repeatedly piled up and then flattened until the deslimer is evenly mixed with the excavated tailings;
[0035] Put the mixed excavated tailings at room temperature for 6 hours to make the deslimer fully react with the soil particles in the excavated tailings;
[0036] After the standing time is sufficient, use the excavator to load the excavated ...
Embodiment 2
[0040] The total amount of crushed stones and tailings generated at the tail end during the early mining and processing of rock stripping tailings is about 6:1 (soil content 14.3%). The total amount of gravel is about 1,350 tons, of which the total amount of soil is about 193 tons, and a total of 29 tons of desliming agent is added according to the proportion of 15% of the total amount of soil in the excavation tailings area;
[0041] Use an excavator to dig a 5m×5m×1m large pit in the center of the tailings excavation area, add 29 tons of deslimer to it, and then use a forklift and excavator to excavate the tailings The tailings in the area are repeatedly piled up and then flattened until the deslimer is evenly mixed with the excavated tailings;
[0042] Put the mixed excavated tailings at room temperature for 8 hours to make the deslimer fully react with the soil particles in the excavated tailings;
[0043] After the standing time is sufficient, use the excavator to load the...
Embodiment 3
[0047] The total amount of gravel and tailings generated during the mining and processing of rock stripping tailings in the early stage is about 4:1 (soil content 20.0%). The total amount of gravel is about 600 tons, of which the total amount of soil is about 120 tons, and a total of 24 tons of desliming agent is added according to the proportion of 20% of the total amount of soil in the excavation tailings area;
[0048] Use an excavator to dig a 5m×5m×1m large pit in the center of the tailings excavation area, add 24 tons of deslimer to it, and then use a forklift and excavator to excavate the tailings The tailings in the area are repeatedly piled up and then flattened until the deslimer is evenly mixed with the excavated tailings;
[0049] Put the mixed excavated tailings at room temperature for 12 hours, so that the deslimer fully reacts with the soil particles in the excavated tailings;
[0050] After the standing time is sufficient, use the excavator to load the excavat...
PUM
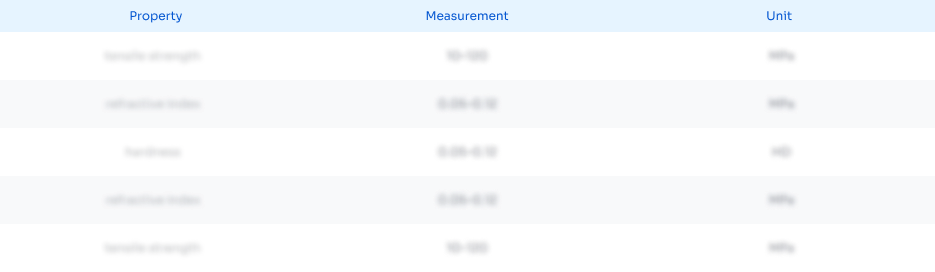
Abstract
Description
Claims
Application Information

- Generate Ideas
- Intellectual Property
- Life Sciences
- Materials
- Tech Scout
- Unparalleled Data Quality
- Higher Quality Content
- 60% Fewer Hallucinations
Browse by: Latest US Patents, China's latest patents, Technical Efficacy Thesaurus, Application Domain, Technology Topic, Popular Technical Reports.
© 2025 PatSnap. All rights reserved.Legal|Privacy policy|Modern Slavery Act Transparency Statement|Sitemap|About US| Contact US: help@patsnap.com